王向明院士:实现增材制造规模化应用,引领该领域技术发展方向
习近平总书记在给航空工业沈飞“罗阳青年突击队”的队员们回信中提到,“希望你们继续弘扬航空报国精神,心往一处想,劲往一处使,在推动航空科技自立自强上奋勇攀登,在促进航空工业高质量发展上积极作为。”回信寄托了总书记对航空人的殷切期望,更指引着攀登科技高峰的前进方向。本期内容来自航空工业沈阳所王向明院士。
鹘鹰战机常务副总设计师王向明院士
航空科技自立自强,既是我们为之努力的奋斗目标,更是引领我国航空武器装备赶超世界先进水平的核心竞争力。
历史经验告诉我们,航空事业新篇章只能由中国人自己书写,核心技术是买不来、讨不来的,自立才能自强,自强才能制胜。航空武器装备是现代战争的首战装备、核心装备、决胜装备,只有自立自强,才能持续不断地研发出高质量“制胜”装备。航空工业从抗美援朝的烽火硝烟中走来已七十余载,历经艰难曲折,新中国的飞机设计事业也历经了一个甲子。面对千沟万壑、艰难险阻,一代又一代航空人不畏困难、锐意进取、自立自强、航空报国,推动我国航空武器装备努力追赶航空强国,实现了从望尘莫及到望其项背,再到同台竞技的历史性跨越,为我国强大空军建设提供了有力保障。
航空科技自立自强,需要科技创新作为核心支撑。
航空科技创新的源头在于设计,因为设计是主导、材料是基础、制造是手段、维修是保障。这些年,航空工业沈阳所在增材制造创新应用、飞机新概念结构领域开拓、新机快速试制模式构建等方面取得新突破,走出一条独具特色的设计制造一体化创新之路。在中型四代机验证机中突破了传统极限束缚,打破了传统结构的“天花板”,大幅度减少零件和工装数量,实现重量偏差精准控制,并率先实现增材制造规模化应用,引领着该领域的技术发展方向。
科技创新的实践经验告诉我们,研制高端的航空武器装备只有自主创新一条路可走。
我们只有持续创新,才能在科研的道路上走得越来越笃定,越来越有信心。面向未来,要继续坚持航空自主创新道路不动摇,健全创新机制,补齐短板,建立新机快速研制新模式,加速创新人才和业务尖子的培养,通过军地融合,搭建更多创新平台,持续解决核心技术攻关难题,积极支撑航空武器装备高质量发展。我们坚信,广大航空科技工作者一定会以习近平总书记给沈飞“罗阳青年突击队”队员们的回信精神作为源动力,学习罗阳同志,弘扬航空报国精神,发扬航空人艰苦奋斗、忠诚奉献的优良传统,踏实钻研前沿技术,心无旁骛,匠心如一,向着建设新时代航空强国的宏伟目标努力攀登、奋勇前进。
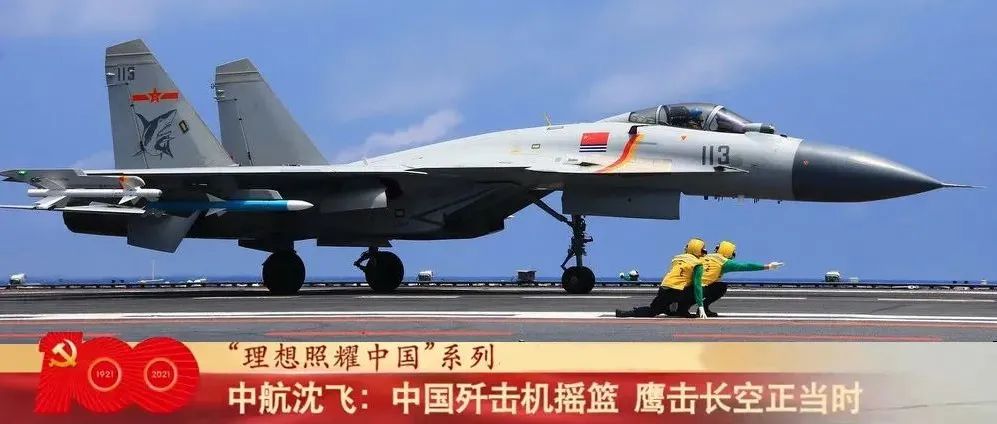
王向明院士借助在原总装先进制造专业组担任增材制造责任专家的机遇,规划出基于增材制造的大型整体化、构型拓扑化、梯度复合化和功能结构一体化等飞机新概念结构领域,主导系统级技术开发与工程化验证。
2021年,中国工程院公布2021年新增院士,中国航空工业集团公司沈阳飞机设计研究所项目总设计师、3D打印专家王向明成功当选。
主编微信:2396747576;硕博千人交流Q群:248112776;网址:www.amreference.com
延伸阅读:
1.技术拐点助力战机跨代!3D打印在我国战机上实现了规模化和工程化应用
3.「3D打印态」钛合金具有均匀且不间断的柱状晶,获得良好的抗蠕变和抗疲劳性