3D打印在燃料喷嘴组合制造中的应用潜力与优势分析
www.amreference.com
众所周知,GE公司自2015年已经使用增材制造技术批量生产发动机燃油喷嘴。与之前传统加工零件模型相比,增材制造的组合喷嘴的耐久度提高了5倍,且增材制造技术将之前20个零件组合为1个单独组件,减少了传统加工工艺中必须使用的焊接技术。这种燃油空气组合喷嘴已经用在LEAP等发动机上。
燃油空气组合喷嘴工作过程
由于增材制造技术在过去几年持续受到重视,燃油喷嘴的组合设计和增材制造方案也开始被包括中国在内的很多国家尝试。本期,我们介绍航发院杨谦研究员关于3D打印在燃料喷嘴组合制造中的应用潜力与优势分析。
发动机燃烧室最关键的一个组件
燃料空气组合喷嘴是燃烧室中最关键的一个组件。它的作用是使液态燃料形成良好的雾化颗粒群,对液态/气态燃料和空气进行高效混合,在燃烧室头部产生稳定火焰的回流区,生成的旋流火焰满足燃烧室的点熄火、燃烧效率、排放物和出口温度指标要求。
目前,先进的燃料空气组合喷嘴往往采用燃油喷嘴+单级或多级旋流组件组成,燃油喷嘴流道和旋流空气流道结构复杂,采用传统制造方法零件数量和加工工序较多,增材制造加工技术的出现为喷嘴生产制造提供了一个优化路径。
正在打印中的喷嘴
另外,增材制造个性化制造的特点在异形组合喷嘴的加工上也得到了应用。无人飞行装置的动力系统在使用高能量密度燃料时会出现燃烧系统低效能的情况。为解决微尺度燃烧室效率和耐久性问题,表面积与体积比率很高的微型燃烧室多采用微尺度和中等燃烧尺度燃烧组织方式,应用传统的制造工艺面临诸多困难。
采用金属3D打印技术成功制造多个4×4中等尺度的受控旋流阵列组合喷嘴,充分验证了该技术加工小型复杂高纵横比零件的可靠性和可重复性。但在加工过程中也出现了一些不足和问题,如孔形变窄、通道塌陷和结构加工不完整等情况。奥地利Combustion Bay One团队为了降低旋流通道的压力损失,优化旋流喷嘴的流动燃烧性能,设计出多个使用数学分析手段得到的螺旋式旋流器。在进行评估之后,采用SLM技术完成了IN718材料的旋流器加工。据统计,一个旋流器的平均加工时间为10h,壁面厚度最小可以达到0.5mm,且在加工过程中不需要额外的支撑结构。
增材制造在异形组合喷嘴加工的应用,加工过程无需支撑
同样,利用增材制造技术进行燃油喷嘴和旋流器制造的还有赛峰直升机发动机公司、西门子公司和Euro-K公司等。在满足制造精度的前提下,增材制造技术使得制造工序大大减少,有效地缩短了生产周期,降低了成本。
传统加工面临的挑战有哪些
燃料空气组合喷嘴航空发动机对燃烧室性能要求的提高使得燃烧室头部的燃烧组织方式发生了较大的改变。从传统的燃料空气组合喷嘴进一步发展出了中心分级头部燃烧组织方式。由于燃料空气组合喷嘴的设计需遵循强化混合的目标,燃料流动通道和空气流道在上游分隔而下游合并,燃料流速较空气更高,因此,流道尺寸小,空气量相对大且需确保均匀,往往采用轴对称的尺寸相对较大的旋转结构,这些特点使得燃料空气组合喷嘴的结构异常复杂。
喷油嘴头部复杂结构
在加工过程中,由于小孔、燃料管道、旋流叶片和复杂混合腔道的存在,需要将喷嘴分拆为多个零件进行加工。在加工和装配的过程中,还需要设计多个工序来保证尺寸、精度、粗糙度和密封性的要求。而且,分级喷嘴的出现,使得燃油流道和空气流道的个数进一步增加,燃油流道由1~2级变为2~4级,空气流道由2~3级变为3~6级。同时,具体结构的尺寸差异也在放大。采用传统加工方式,组合喷嘴分拆出的零件数量将会由5~10件增加到20件以上甚至更多。由于结构复杂性的增加,零件的装配和焊接会遇到巨大的困难,需要进行精细的结构设计来避免装配问题的发生。
增材制造技术的应用潜力及优势分析
增材制造技术应用在燃料空气组合喷嘴上将会大大促进喷嘴研制的发展。其应用在喷嘴研制领域的优势体现在以下几个方面。
一是减少加工装配工序的个数。由于增材制造技术是一次成型的制造技术,在进行喷嘴生产的过程中只需要提供符合设计要求的喷嘴3D模型就可以一次性加工得到。
二是可以实现多种复杂结构的设计方案。对于传统加工方法很难做好的多级旋流结构、油气混合腔道和吹扫空气结构等,增材制造技术通过模型生成都可以做到。
南科大基于增材设计的航空发动机燃油喷嘴剖面图
三是保证密封要求。由于不存在焊接工序,燃油和空气流道的密封性可以得到更好的保证。
四是尺寸精度更高。增材制造技术的最高精度在μm量级,完全能够满足尺寸在mm量级上的喷嘴加工限制要求。
五是加工周期短。由于增材制造技术工序的减少,增材而非减材的方式注定了其加工用时大多短于传统机械加工方式。
国内设备商打印的航空燃油喷嘴
END
近年来,国内中科院、西工大、南科大、中国航发等单位针对燃油喷嘴的组合设计和增材制造研究也取得了很大进展。这些进步不仅包括结构设计方法和制造工艺,还涉及抛光等后处理方案以及可靠性验证研究。经过优化设计和SLM成形的喷嘴壳体简化了装配和焊接等加工工序,缩短了制造周期,流道成形精度高,达到了减轻重量和改善性能的目的。但我们都知道,如此重要的部件,还需要经过实际应用的检验。
2.3D打印集成制造的最佳实例:从855个零件到12个零件的非凡效益
3.3D打印实现制造轻量化(二):优化设计,降低材料使用要求
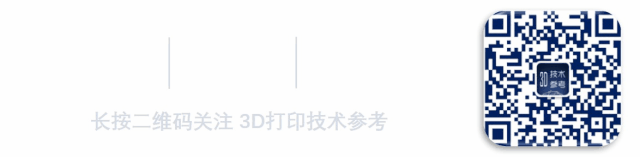
原文始发于微信公众号(3D打印技术参考):3D打印在燃料喷嘴组合制造中的应用潜力与优势分析