应用行业渗透:宝马将使用电弧增材制造生产汽车部件

宝马集团长期以来一直是增材制造技术的用户和创新者。3D打印技术参考跟踪了该公司最近几年在3D打印技术领域的应用进展,尤为突出的是,它已经实现了塑料、金属和砂型3D打印的初步自动化制造。大约在2015年,该公司开始关注电弧增材制造技术(WAAM),根据最新的消息,宝马计划从明年开始在车辆中测试电弧增材制造的零件。
电弧增材制造技术与其他金属3D打印及传统制造工艺不同,它利用通过电弧熔化的金属丝来实现层层制造。该技术能够创建中空结构,生产出具有卓越刚性重量比的部件,超越了通过传统压铸方法生产的零件性能。这不仅可以使零件变得更轻、更坚固,而且还可以降低能源需求并最大限度减少材料浪费。
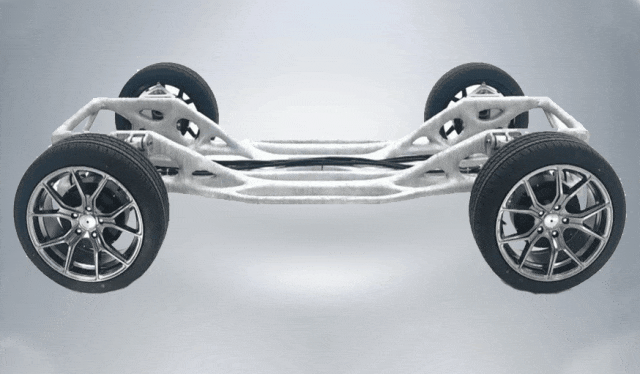
铝是汽车制造的首选材料,同时,铝合金也是电弧增材制造最重要的成型材料之一。根据3D打印技术参考的技术案例积累,知名民营航天公司Relativity Space使用铝合金电弧增材制造技术来打印燃料贮箱结构;西工大也曾发文指出,其高性能铝合金电弧增材制造基础研究为梦天舱和长五B的研制提供了重要技术;首都航天机械有限公司开发的铝合金电弧增材制造技术被用于制造捷龙三号重要部件,该火箭于2022年底成功发射。总的来说,铝合金电弧增材制造工艺目前已经是较为成熟且可靠的制造技术。
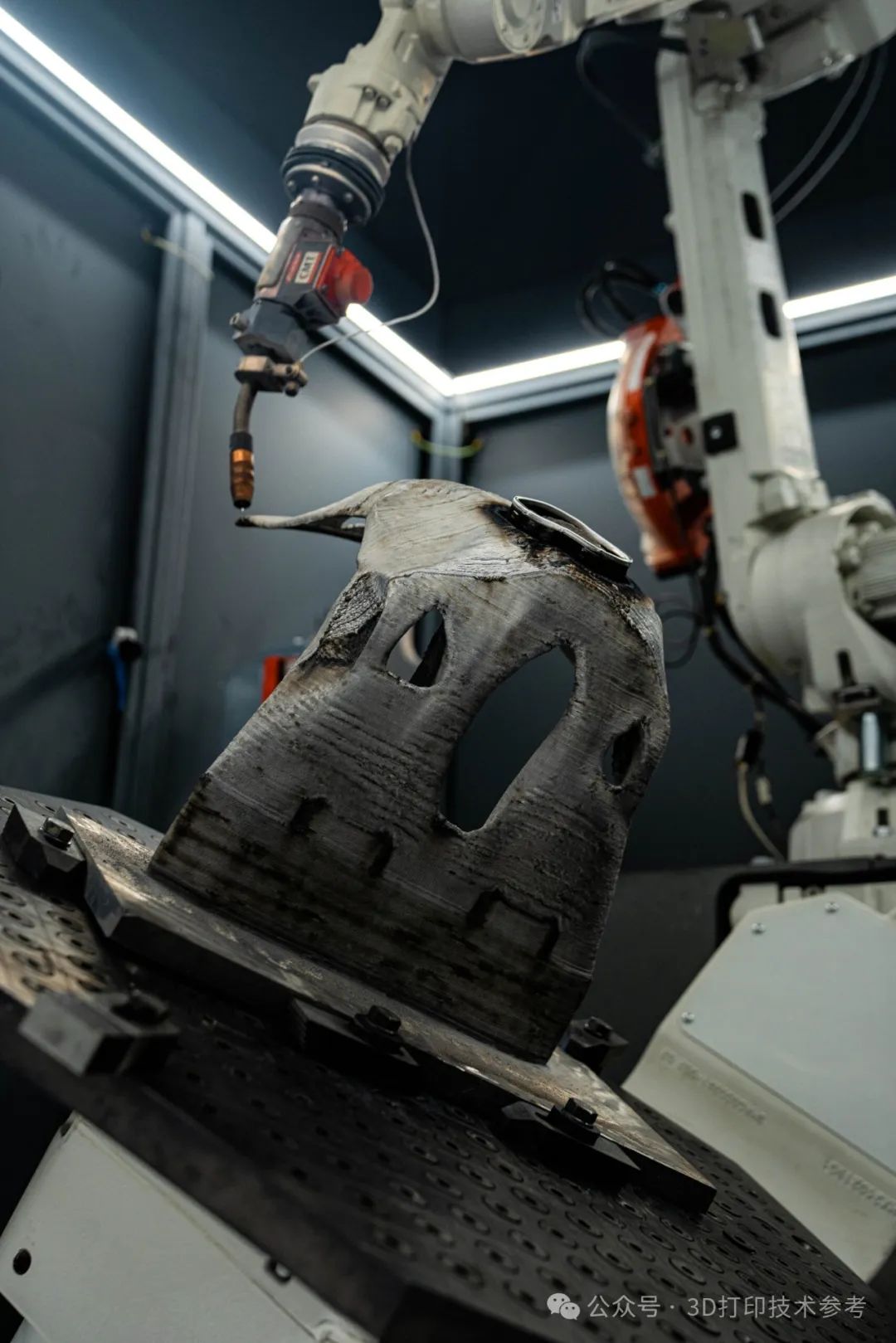
宝马电弧增材制造的零件
仍然遵循从高端行业应用开始,逐步走向其他行业的特点,铝合金电弧增材制造技术开始延伸到汽车制造行业。宝马于2015年开始探索WAAM,并于2021年安装机器人单元。粉末床熔融3D打印工艺(宝马现已将其转变为自动化流程)非常适合较小的零件,而WAAM技术更适合车身、驱动器和底盘中的部分。因此,该公司使用该技术3D打印了一个悬架支柱支撑件,并将其与压铸件进行匹配。
“在早期阶段,WAAM工艺可以降低生产过程中的排放量,这一点已经很明显。组件重量较轻,材料利用率优越,并且可以选择使用可再生资源,这意味着可以更高效的生产组件。”宝马增材制造主管JensErtel表示。
WAAM悬架支柱的衍生式设计图纸
为了创造用于车辆的最佳零件,宝马转向衍生式设计。与仿生结构的原理类似,第一步涉及仅利用组件拓扑所需的基本材料。在随后的微调阶段,仅在需要的区域选择性的进行加强。需要特别指出的是,这类仿生组件也许能够通过铸造手段实现,但组件的强度却无法达到3D打印的组件强度;而如果使用锻压,则无疑成本过高。由Relativity Space开发的火箭仿生组件说明了这一特点。
RelativitySpace开发的火箭仿生组件
“WAAM技术已经开始从用于研究发展成为一种灵活的工具,不仅适用于制造测试组件,还适用于批量生产组件。生成设计方法的使用使我们能够充分利用设计自由度,从而充分利用技术的潜力。就在几年前,这还是不可想象的。”宝马集团汽车研究主管Karol Virsik表示。
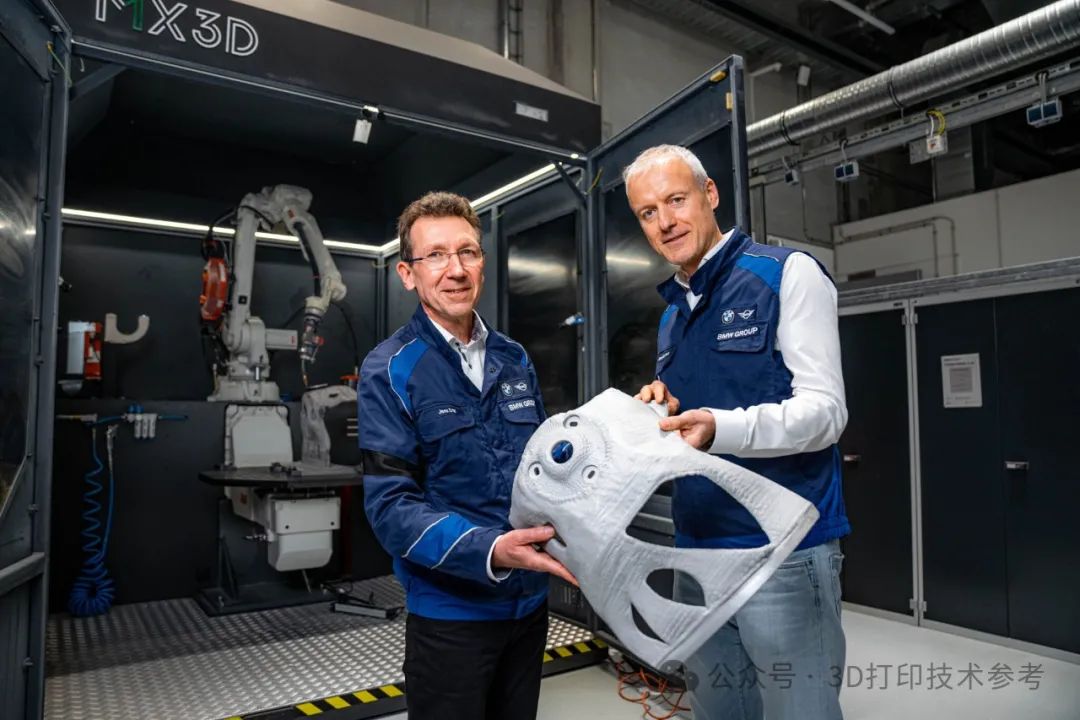
正如宝马通过政府支持的财团解决其他3D打印技术的精加工需求一样,该汽车公司可能也需要对WAAM零件做同样的事情。由于焊缝较宽,这些部件具有独特的波纹表面,因此需要对关键区域进行额外的精加工。
但工艺的发展往往超出人们想象。大部分人对电弧增材的印象仍停留在该工艺效率高但制造的零件表面非常粗糙,只能打印大尺寸零件。长时间以来,市场上电弧增材的实际应用大多如此——成型尺寸大、需要后续机加改善表面质量。但3D打印技术参考在2023年底已经报道过,国内领先的电弧增材制造厂商英尼格玛,不断打破工艺极限,已实现大尺寸零部件精细化打印。
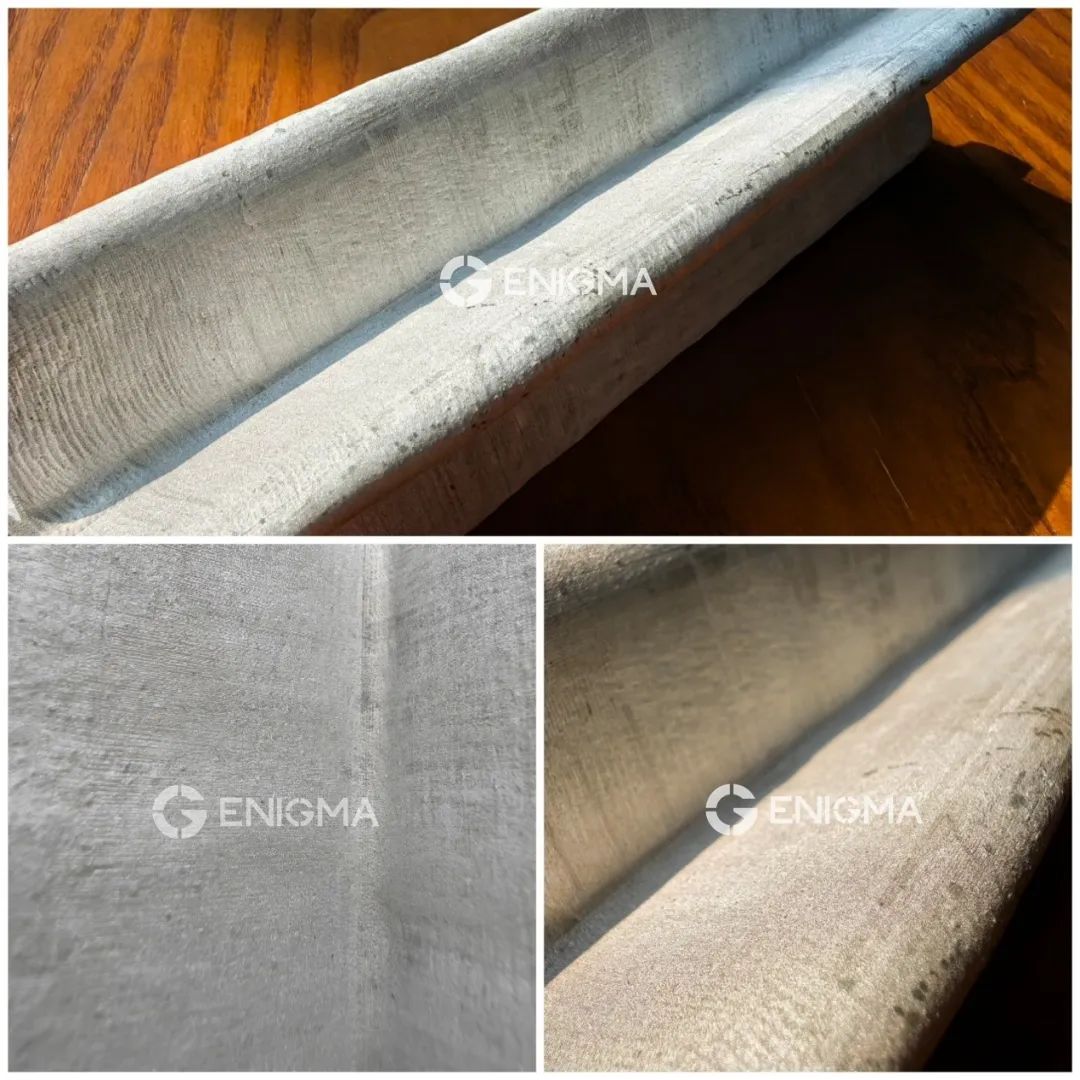
另一方面,铝合金电弧增材制造的质量也是影响零件能否最终应用的关键。电弧增材工艺对过程控制条件要求极高, 而气孔是铝合金增材制造过程易出现的主要缺陷之一。气孔会降低材料致密性,削弱有效截面积,严重的话甚至会影响产品的性能和品质。据了解,为了解决该行业难题,融速科技研发团队经过数百次技术验证取得突破,研发出了高效铝合金气孔抑制技术,符合HB963一级标准。融速科技电弧增材平台AMmake S2系列所采用的该技术生产的零部件,即能够规避传统铝合金制造工艺中的气孔缺陷等。
融速科技铝合金电弧增材制造气孔抑制技术
融速科技铝合金电弧增材制造零件
最初,宝马集团打算将WAAM零部件生产集中在增材制造园区。然而,未来计划将生产扩大到更多地点,并使供应商也能够利用这项技术。此外,还可以将该流程直接集成到装配线中,从而无需使用新工具,只需更新软件即可创建独特的组件并生产各种零件。此外,通过增加回收金属的使用,可以进一步增强该过程的可持续性。完成测试评估后,初步车辆试验计划于2025年开始。
主编微信:2396747576(请注明身份);硕博千人交流Q群:248112776;网址:www.amreference.com
延伸阅读:
2.重大突破,打破封锁!国产多光束集成丝光同轴激光定向能量沉积技术!
4.国内电弧增材制造技术正在爆发,或在复制SLM技术的成功之路