传统加工技术的代表企业GF推出更加完整的增材制造解决方案
www.amreference.com
随着材料技术的进步,增材制造行业已经从快速原型制作过渡到最终产品直接制造的发展阶段。然而真正产品化却远比我们想像的复杂:在产品的制造过程中如何确保各工艺的顺利衔接?如何减少后处理过程中的大量人工操作?如何保证在此过程中稳定一致的产品质量?增材制造能否可以进一步提高效率、降低成本?
对此,精密加工界的知名品牌GF与3D Systems合作率先推出了面向增材制造的整体解决方案,以推动传统技术与增材制造高效整合和各工艺环节的无缝衔接。
本期,3D打印技术参考来介绍GF的增材制造解决方案及其背后思考。
完整的金属增材制造流程包括了从设计、材料、工艺到后处理的所有制造环节。采用增材制造技术生产的零件,尤其是金属零件几乎都需要经过后处理才能使用,而这在前端设计的时候就需要考虑到工件在不同工艺之间流转会遇到的加工余量、结构倾斜以及应力避免等问题,复杂零件的CNC加工也需要运用专门设计的夹具。这实际上要求应用端的从业者既要懂得传统机加的特点,又要懂得增材制造。
接下来我们以法国宇航公司TAS的卫星天线支架为例阐述GF如何解决上述问题,并帮助终端用户真正生产出高品质的金属3D打印零件。
TAS的卫星天线支架重新设计并3D打印
卫星在发射过程中为防止天线结构振动断裂会将其固定在支架上。对于此类用量并不会很大的零件,采用3D打印制造的成本自然要比传统技术低很多。然而直接按照传统加工的习惯去设计和制造支架,就无法体现金属增材制造的优势,在打印过程中还会有出错的风险,而且也要考虑到后续的铣削加工和零件的功能。对此,GF提出了从软件设计准备,到设备打印,再到质量控制,以及后续铣削加工和线切割的7步走方案,决议采用全流程思维重新定义零件制造。
-- 设计 --
面向增材制造的设计需要我们从增材的工艺需求出发,摒弃机加工设计时的惯性思维。在此案例中我们就可以看到多项设计思维上的调整,包括将水平悬垂调整至45°,为避免应力将尖角进行倒角,为减少铣削时间同时减少干涉进行铣削设计,以及为提高整体刚度进行的功能性改进设计等等。
依据增材思维设计的零件,可以尽量多的避免支撑结构,获得更好的局部表面质量,并降低应力集中的风险。
-- 打印准备 --
打印准备过程包含了支撑添加以及零件排布等工作;特别值得一提的是GF在基础打印基板之上设计了16块专利的换装夹具(小基板),零件可以直接在上面进行打印。
在机加过程中,小基板可帮助迅速找到零点,而且便于快速装夹,提高了增减材之间的衔接效率,确保零件批量生产时获得一致的精密度,这一步也为未来的自动化奠定了基础。
-- 打印--
打印此卫星支架所用到的DMP Flex350是为高精度直接金属打印而设计,利用其业内含氧量最低的真空打印仓及改进的气流技术确保每一个零件打印出来的致密性和力学要求。
-- 质量控制 --
打印过程的关键之处在于质量控制和可追溯性,GF专门针对复杂和重型金属部件的关键应用进行了优化,同时会记录材料特性和完整的打印过程。
-- 后处理 --
增材制造的后处理通常是指线切割、零件抛光和机械加工。与目前常见的垂直切割方式不同的是,GF的CUT AM 500采用水平切割的方式,完全避免了零件切割时发生碰撞的可能性,有效提高了去除底板的效率及可靠性,特别适合大型零部件和批量生产的工件。
CNC文件的准备如规划加工高质量的曲面区域、钻孔、攻丝或修整孔等,在最初准备打印文件的3DXpert软件中就可以完成,其CNC加工能力完全承自传统行业使用的Cimatron软件。在机加工过程中所面临的余量设计,实际上也在上述软件中进行预留,零件的底部也配合了System 3R零点定位系统,可以进行快速装夹,实现自动化生产。
END
总结以上步骤,我们可以看到,增材制造技术更适合生产难加工、需要大量切削的零件,如何高效整合和连接各个工序是增材制造方案是否出色的关键。增材制造必须与其他传统制造工艺相结合,才能成为创造制造业附加值的“利器”,才能成为制造产业化的主旋律。
GF加工方案推出的行业领先的整体解决方案,无论是在传统减材行业还是现在市面上常见的3D打印大玩家们都不具备的,我们有理由相信这一前瞻性的探索会极大的推动增材制造的批量化生产应用之路。
注:报名参加GF 加工方案增材制造在线研讨会
https://wj.qq.com/s2/5684484/9dc9/
3.【增材制造】保证产品质量及批量生产的稳定性-FAA是怎么做的
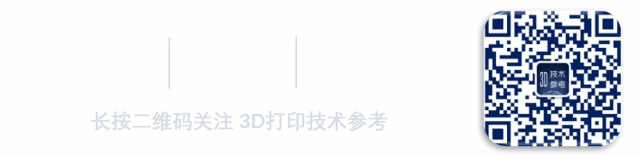
原文始发于微信公众号(3D打印技术参考):传统加工技术的代表企业GF推出更加完整的增材制造解决方案