近日,南京航空航天大学顾冬冬教授等人回顾了近年金属零件激光增材制造技术在高端领域的应用研究,系统地讨论了激光增材制造组件在航空航天、汽车、生物医学和核能行业的应用和未来发展。相关总结和评述于2023年1月27日在线发表于《Laser Additive Manufacturing of Metallic Materials and Components》。
原文链接:https://doi.org/10.1016/B978-0-12-823783-0.00016-4
激光增材制造在航空航天工业中的应用
航空航天增材制造的应用场景包括大型金属部件、复杂集成结构、轻质晶格结构的增材制造。在该领域,顾冬冬教授发表过《航空航天高性能金属材料构件激光增材制造》一文,因此本部分为避免重复,以增材制造技术前沿的介绍为主。
激光能量沉积和粉末床熔融工艺已经被证明可用于大型金属部件的直接制造。对于激光能量沉积,国内最知名的案例是西工大使用该工艺为商飞C919生产了超过3米长度的TC4合金翼肋条,王华明教授也使用该工艺生产了战斗机使用的主承力框;在国外,NASA使用该工艺制造了大型火箭燃烧室。对于粉末床激光熔融工艺,近年来也得到了极大发展,尤其体现在大尺寸制造方面。当前装备甚至可以打印超过米级的零件,诸如火箭和导弹发动机的燃烧室、发动机箱体,均可以实现高精度制造。在此方面,国内外均有实际案例。
复杂结构集成制造也是航空航天领域增材制造技术应用的重点,尤其以GE航空最为知名。在最新的案例中,该公司合并了150个零件,设计和3D打印了涡轮中心框架(TCF)外壳;此前,它还创造了将300个零件合并为一个经典案例。一体化集成堪称3D打印制造的最佳实践,它是对传统制造方式的重大改变,影响了产品性能、开发方式以及制造相关的方方面面。
轻质晶格结构也是航空航天领域的重要应用,其在卫星蒙皮结构、支架等产品中有大量应用,最直接的优势就是减重。同时该结构当前也已经应用到了民航领域,空客商用飞机的机舱舱壁是近年来的一个成功案例。
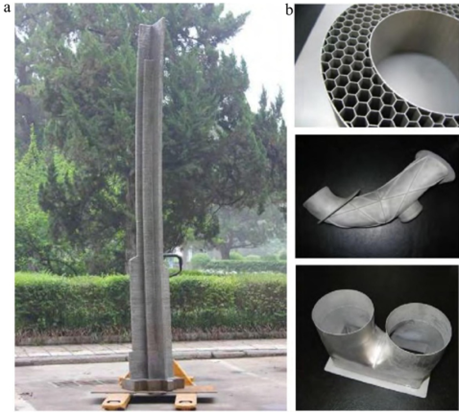
图1 激光定向能量沉积和激光粉床熔融制造大型复杂金属构件
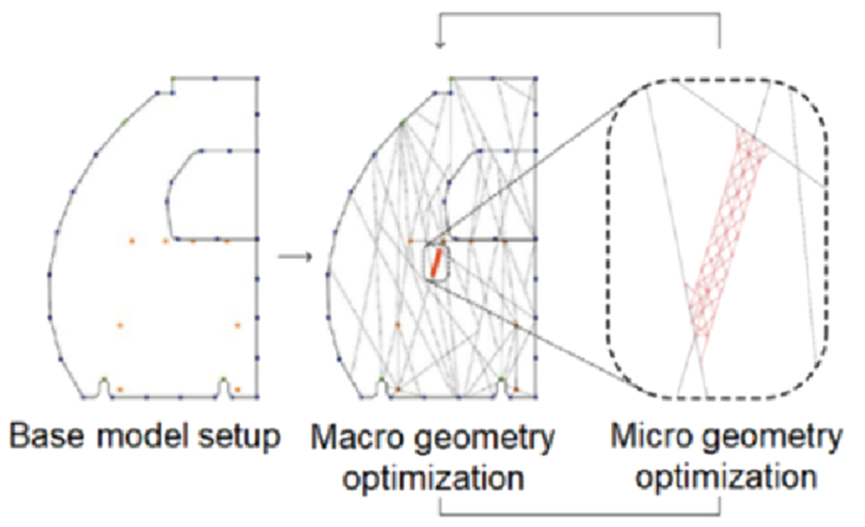
图2 由空客公司设计,激光选区熔化制造的新型客舱隔板
激光增材制造在汽车工业中的应用
汽车工业的燃油经济性对于降低碳排放对环境的负面影响至关重要。使用轻量级组件对于实现这一目标至关重要。拓扑优化在汽车零部件设计中的减重效果明显。重量的减轻与制造阶段的能源消耗减少有关。然而,拓扑优化在特定约束和设计条件进行结构优化设计时,通常不考虑结构的可制造性。这些优化的结构通常很难或不可能用传统工艺制造。激光增材制造(AM)作为一种先进工艺,为复杂拓扑结构的优化提供了自由。拓扑优化和增材制造技术如何结合在一起,为汽车行业的轻量化和低成本结构提供一个良好的选择。拓扑优化之前会采用有限元分析对初始设计的结构安全性进行研究,然后进行拓扑优化,在不增加激光增材制造部件重量的情况下提高其结构效率。研究人员利用AlSi10Mg合金低密度、高抗拉强度的特点,制备了一对优化后的构件,如图3所示。
图4a是布加迪采用LPBF技术进行电机支架的系列生产,该电机支架具有集成水冷,起到主动热屏蔽的作用,可以显著减少热量传递,目前该发动机支架已安装在所有系列车辆上。图4b是奔驰采用激光增材制造技术制备的零部件。图4c是刀具增材制造的实验程序,对刀具表面进行抛光,以保证工业实践通常要求的粗糙度。试验结果表明金属增材制造可以为冲压工艺提供性能优良的刀具,并显著缩短加工时间。此外,激光增材制造技术在压铸随型冷却通道设计方面也取得了突破。减小冷却通道与压铸表面的距离,以一致的速率散热促进散热均匀性,图4d。
使用高精度Trumpf TruPrint 3000设备制造了保时捷活塞,如图5所示。该过程从利用激光增材制造对活塞进行拓扑优化,每个活塞都比批量生产的锻造活塞轻10%。6个活塞安装在3.8L双涡轮发动机上,进行耐久性测试。在满载情况下运行了135小时,在不同速度的拖动负载下运行了25小时。经过200小时的测试,不仅6个活塞都通过了严格的测试,而且这些铝活塞也有潜力与铸造或锻造的活塞相匹配甚至超越。事实上,保时捷并不是唯一一家研发增材制造组件的汽车制造商。布加迪工程师采用激光增材制造技术制造出制动卡钳,比以前使用的制动卡钳轻5磅,如图5所示。
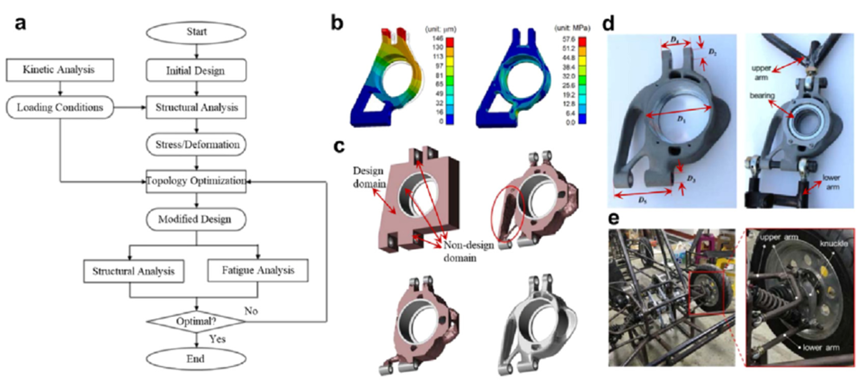
图4 汽车工业中金属部件和工装的激光增材制造零件:(a) 激光增材制造技术加工的布加迪电机支架;(b)小批量生产奔驰正品替换件;(c)刀具增材制造程序;(d)冷却模具的设计和激光加工
图5 激光AM金属零件的验证:AM加工的保时捷发动机活塞耐久性试验
激光增材制造在生物医药行业中的应用
由于激光增材制造具有专为患者设计、复杂性高、生产率高、成本效益高等优点,在生物医学领域得到了广泛应用。增材制造在生物医学中的主要应用包括组织工程模型、解剖模型、药理设计和生物医学仪器。与传统的医疗器械制造技术相比,激光增材制造技术是一种具有发展前景的新型医疗器械制造技术。根据患者的临床图像,利用激光增材制造技术可以高效、准确地制造出定制的医疗器械和手术导板。此外,激光增材制造可与多种生物相容性材料兼容,如锌合金、钴铬合金、钛合金等,被广泛应用于植入物和矫形器/假体制造。
工作流程包括四个步骤:医学成像、3D建模、增材制造和临床应用。图6a是从医疗数据到最终增材制造的工作流程。激光增材制造的另一个好处是它能够制造复杂的轻质形状,如晶格结构。图6b是基于三周期最小表面设计的多孔金属生物材料具有低弹性模量、远超皮质骨强度的高屈服强度和超长疲劳寿命,耐久极限超过其屈服强度的60%的理想组合。为了设计生物材料和骨科植入物的小尺度几何形状,可以使用骨组织适应模型或拓扑优化算法。这促进了植入物的合理设计,因为仿骨生物材料或植入物不是通用的,而是针对特定患者的特定机械负荷条件。
图6c是采用激光增材制造技术用于固定面部轮廓,恢复正常的外观和功能。激光增材制造技术的能力,如快速生产患者特定的植入物,减少患者的创伤,并通过更短的手术时间提高手术的成本效益,从而使患者更快地恢复,通过该应用得到了证明。图7是使用增材制造技术设计和打印的生物植入物的示例,包括单胞CAD模型和增材制造制胞状结构。这个案例表明增材制造技术可以开发最接近曲面的晶格结构。同时,利用增材制造技术制造的金属生物医用植入物的骨整合表面可以避免应力屏蔽现象,促进骨的长入。
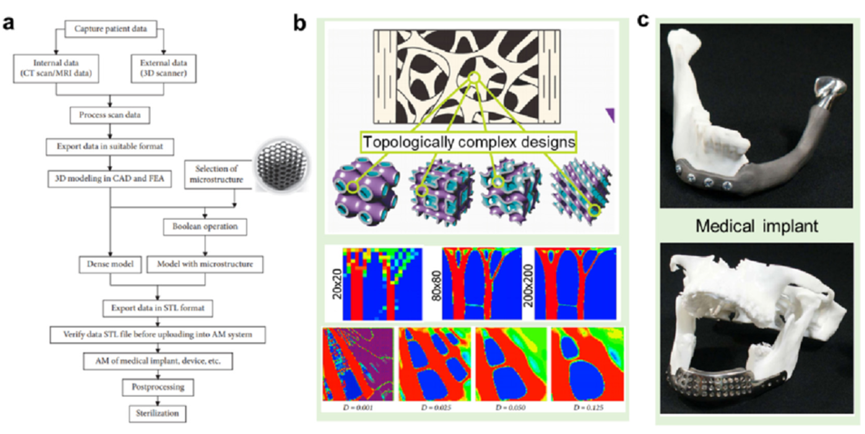
图6 生物医用金属植入物的激光增材制造:(a)从生物医学数据到最终部分的流程图;(b)基于三周期最小曲面和拓扑优化的增材制造金属多孔种植体;(c)由Ti6Al4V制作的下颌骨种植体
图7 (a)种植体和细胞结构的CAD设计;(b)人造髋关节假体。
激光增材制造在核能工业中的应用
用于核反应堆应用的材料有严格的性能要求,必须能够耐受极端环境,包括高温、辐照和在受到机械应力时与腐蚀性介质接触。增材制造已被证明可以制备许多类型核材料部件。这些零件可用于国际热核实验反应堆的冷却系统。该模型具有特定的几何形状,包括薄壁(以加强热交换)和内部冷却通道。薄壁模型的一个例子如图8a所示。图8b是经过36小时的LPBF加工,具有内部冷却通道的预制件,平均气孔率约为1%。另一个例子是带有内部铜冷却通道的不锈钢组件,其中氦气将被用作冷却剂。为了提高换热元件的换热系数,内表面必须具有特定的几何形状。也有研究人员使用PHENIX-100机器通过增材制造技术制造了这种双组份物体(不锈钢/铜),经检测,零件无孔洞、裂纹等缺陷(图8b)。
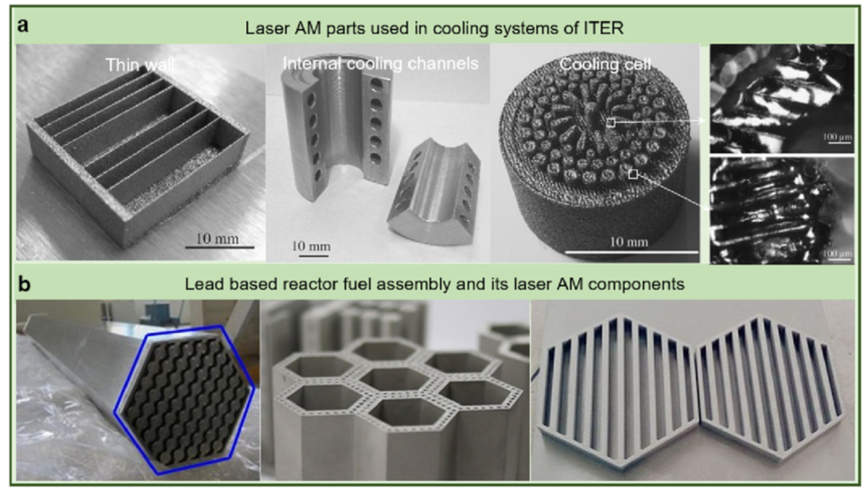
图8 激光增材制造加工的核能部件:(a)用于冷却系统的激光增材制造薄壁集复杂模型;(b)铅基反应堆燃料组件及其增材制造组件
总结和展望
(1)设计自由、制造复杂结构的能力是激光增材制造技术的主要优点。随着这一技术的进步,已用于各种高端应用,包括航空、航天、汽车、生物医学、核能等。
(2)最近的发展表明,激光增材制造能够制造具有不同金属材料、复杂结构和优异力学性能的接近全密度的金属部件。
(3)材料、结构和性能的一体化对于追求高性能和轻量化零件很重要。激光3D打印技术在制造一些典型金属结构及其在航空航天、汽车、生物医学和核能领域的应用方面已经开始展现出巨大的潜力和优势。
(4)虽然增材制造技术与传统制造方法相比具有许多优势,但它仍然被大多数高端行业视为一种小众技术。为进一步获得业界认可,需要在设计、材料、新工艺和机器等多方面进行研究和开发,以扩大AM技术的应用范围,并将其提升为主流技术。