SLM-3D打印一体化多金属材料散热器,揭示未来应用潜力
Aerosint自2016年成立以来一直在开发选择性粉末沉积(SPD)技术,该技术可选择性沉积两种(或更多)粉末,形成厚度可调的单独粉末层,能够应用到几乎所有基于粉末床的增材制造工艺中,包括激光粉末床熔融和粘结剂喷射(已被Desktop Metal收购)。
多材料解决方案的应用可以是多样化的,并将随着对新材料的验证而增长。该公司的技术方案目前已经成功应用于SLM技术,并计划将集成到Desktop Metal的P1机器中。2022年,Aerosint还推出了一种无粘结剂的“压制和烧结”方法,使用选择性粉末沉积制造多材料部件。在这个过程中,使用SPD技术将多种粉末填充在模具中,然后进行压制和烧结,这使得制造金属-陶瓷部件成为可能。
激光参数和扫描路径优化
弗劳恩霍夫增材制造技术研究所开发了一个具有多材料的拓扑优化结构的散热器,其具有高度复杂的几何形状,极大减轻了重量,改善了热性能并降低了压降。由于传统技术不可能生产如此复杂的几何形状,增材制造成为首选工艺。
多材料散热器由高强度、耐腐蚀的316L不锈钢外壳和高延展性的CuCrZr铜合金制成,内部具有珊瑚状核心。所选铜合金的导热系数是AlSi10Mg铝合金的2倍、316L不锈钢的16倍,导热效果明显高于其他常见材料。而且,铜基合金是密闭空间散热应用必不可少的材料。
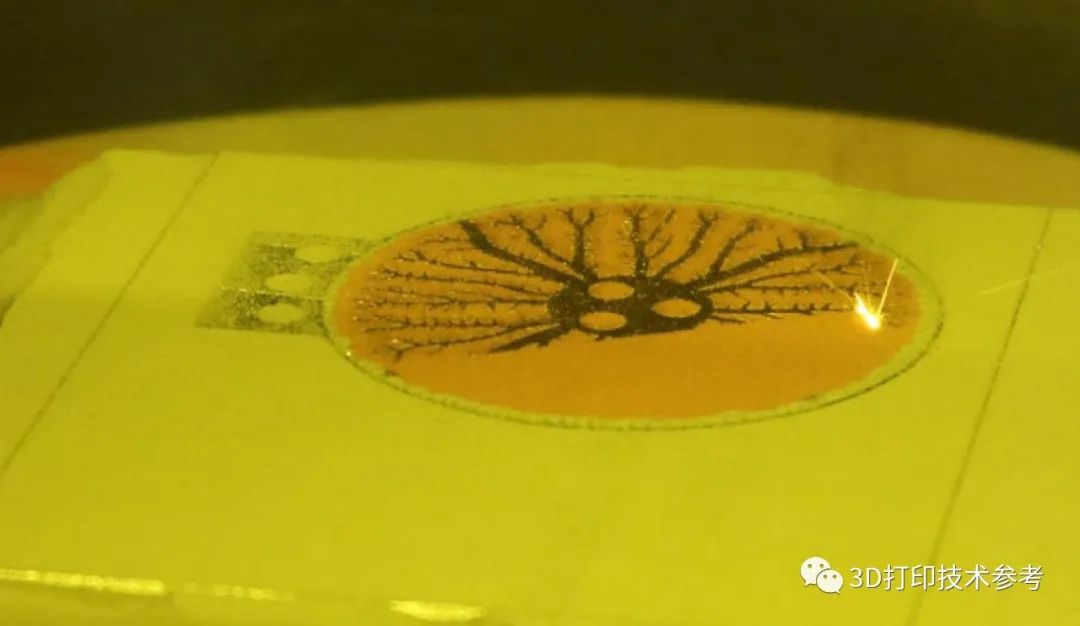
为了能够使用SLM技术实现多材料3D打印,Aerosint的选择性粉末沉积(SPD)系统被安装在Aconity3D 公司的MIDI+机器上。作为双缸单材料铺粉的替代方案,Aerosint的SPD系统的铺粉机构由两个可旋转的转鼓组成,可携带不同粉末,如金属、陶瓷和聚合物。可在构建区域内不同位置上选择性的沉积不同类型的粉末,铺设速度可达50毫米/秒,最小区域尺寸约为0.5×0.5mm2。材料可以单独或连续扫描,可选择不同的扫描策略,优化的激光参数可将两种不同的金属粉末融合在一起,确保在界面处有足够的冶金结合。
3D打印技术参考注意到,配备SPD系统的Aconity MIDI+打印机的构建尺寸目前限制在140×96mm2。
为了达到高导热性,通常必须进行后热处理。Aerosint之前的研究表明,在520°C下保温1小时,炉冷后CuCrZr合金的热导率增加了两倍。在时效过程中,CuCrZr合金中过饱和(Cu)基体上会析出颗粒,达到弥散强化和提高导热性的双重目的。一般情况下,该时效温度和保温时间位于316L不锈钢去应力热处理的窗口内。因此,严格来说,对于本案例中多材料构件并没有必要进行额外的热处理步骤。
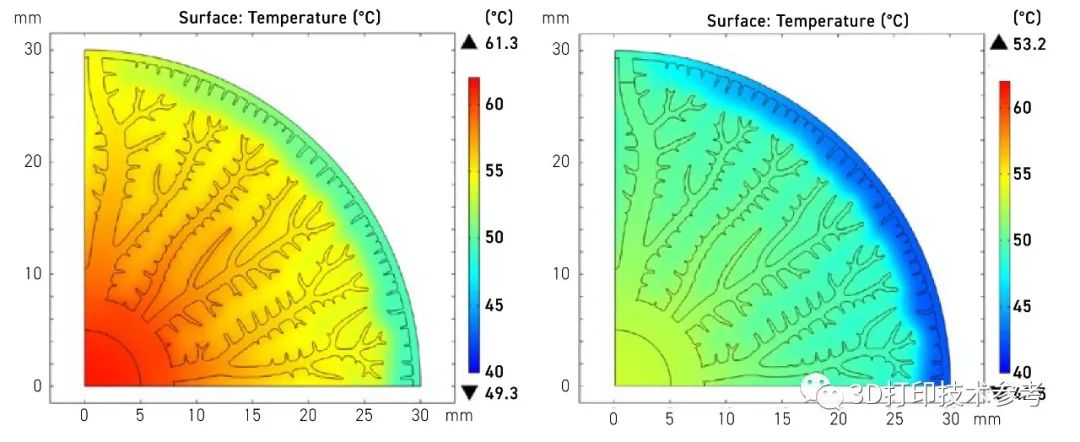
但3D打印技术参考也查询到,一般双金属材料加工而成的零件均需要进行热处理来稳定形状和尺寸,不同的热处理工艺过程对零件的性能影响较大。通过热处理使温度敏感的双金属零件达到尺寸和性能稳定的方法,称为稳定处理。针对双金属零件的具体组成材料、结构复杂程度以及具体的工作环境,会需要不同的热处理手段。
由Fraunhofer IAPT开发并使用多材料3D打印的拓扑优化散热器,证明了多材料SLM技术可以制造具有更高性能的组件。
这种创新的散热器将为汽车和航空航天行业的苛刻应用提供新解决方案。散热和节省空间至关重要,该方案可以提高电子部件的性能和使用寿命。此外,在一种工艺中生产这种多材料、多功能组件显著缩短了交货时间,降低了生产成本。
主编微信:2396747576; 硕博千人交流Q群:248112776;网址:www.amreference.com
延伸阅读:
1.NASA喷气推进实验室公布2022年三项3D打印应用成果
2.行业洞察:高强铝3D打印材料体系、市场化历程及其应用现状
3.重磅分享(二):航空航天增材制造产线建设面临的挑战与要求
4.五千字分享:NASA采用3D打印研制火箭发动机的失败教训与经验