金属、塑料、砂型!宝马完成三类3D打印技术自动化产线建设
当一家公司的3D打印生产规模达到一定程度时,自动化就需要被提上议程。近日,3D打印技术参考注意到,宝马集团新近实施了一项名为POLYLINE的项目,成为首个成功实施大规模聚合物零件自动化增材制造生产线的项目。
需要指出的是,宝马至此已经成功实现金属3D打印、聚合物3D打印以及砂型3D打印的全自动化产线建设!
POLYLINE项目的主要成员包括BMW、DyeMansion、EOS和Grenzebach ,他们在宝马增材制造园区实现了三年前项目开始时的目标:使真正的高吞吐量3D打印批量生产成为现实。
宝马集团增材制造、预开发和规划主管评论道,“POLYLINE自动化流程链适合下一代打印机和我们的标准生产要求,其标准化接口是一种与系统无关的解决方案,这对于扩大增材制造规模至关重要。”
POLYLINE项目汇集了来自德国的15家工业和研究合作伙伴,共同开发下一代数字化生产线,该生产线已用于生产汽车行业的塑料零件。其目的是通过增材制造以高通量生产线系统的形式补充传统生产技术(如机械加工、铸造等)。
该项目由德国联邦教育和研究部资助,总额为1070万欧元。该项目的明确期限为三年。高端汽车制造商宝马集团将POLYLINE项目安置在慕尼黑的增材制造园区,并接管了不同项目合作伙伴的协调工作。
EOS是全球领先的金属和塑料工业3D打印技术提供商,通过其EOS P500 SLS系统提供打印功能,该系统专为高度自动化并集成到现有生产线而开发。EOS P500的自动化和集成水平因每个用例而异,并且可以根据每种情况进行专门调整。在这种情况下,机器确保了最高的可靠性、最高水平的均匀性、重复性和再现性。EOS 聚合物系统主管评论道,“我们在宝马集团和汽车行业开发了这一技术,现在我们可以将其采用并调整到其他行业,”。
作为工业流程自动化领域的专家,格林策巴赫为该项目贡献了其在制造流程智能和安全网络方面的专业知识。格林策巴赫增材制造主管指出,“自动化的主要优点是提高设备的生产率,减少设备的停机时间,并为员工创造一个安全的工作环境。”
在POLYLINE项目中,包括Exchange P500/4解决方案,该解决方案直接安置在打印机上,自动更换打印缸并并冷却刚打印完的缸体,通过安全运输容器和自动导引车,以及带有 KLT处理和箱式拾取机器人的单元,用于进一步处理和分类组件。此外,联合开发适合所有工艺站工业使用的自动化硬件和软件接口是格林策巴赫工作包的核心组成部分。
宝马因此建立了一条数字联网的全自动金属3D打印生产线,并为汽车系列生产做好了准备。通过将金属3D打印集成到汽车行业传统生产线中,IDAM计划每年至少批量生产50000个组件和10000个零配件用于汽车生产,同时保证零件的一致质量并释放目前极高的成本压力。
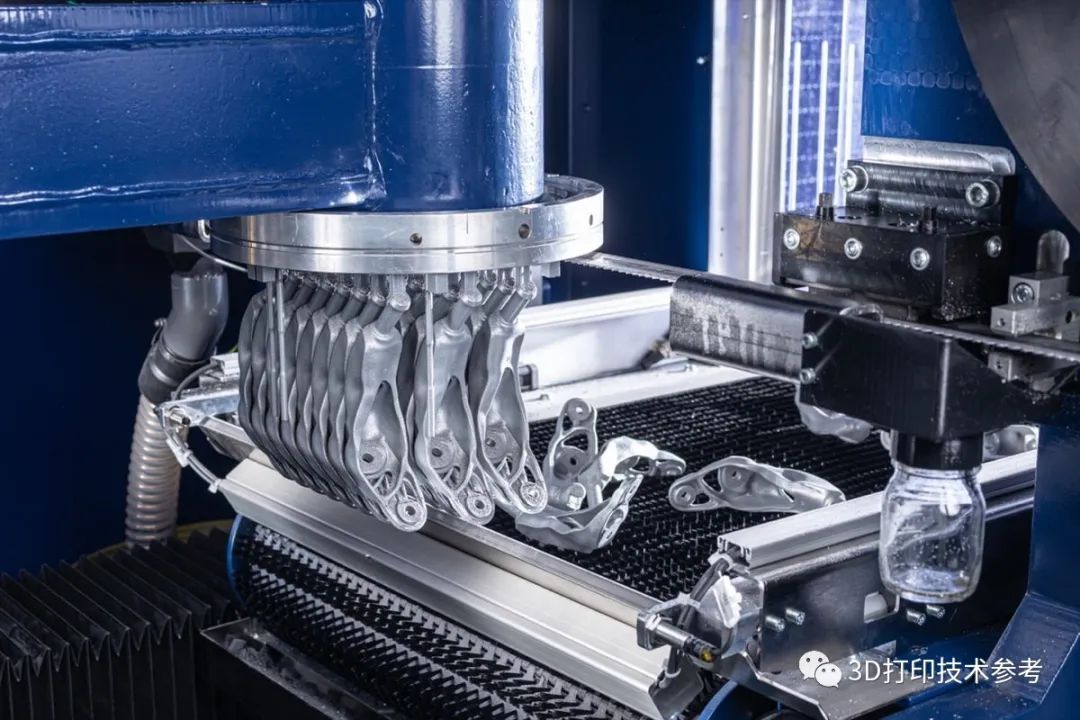
无人驾驶运输系统被集成在IDAM生产线的模块之间,全自动运输3D打印机的移动成型仓。这些机器由中央控制单元进行协调,各个生产线模块的所有生产数据在中央控制单元中汇聚,确保了最高的生产率和质量。
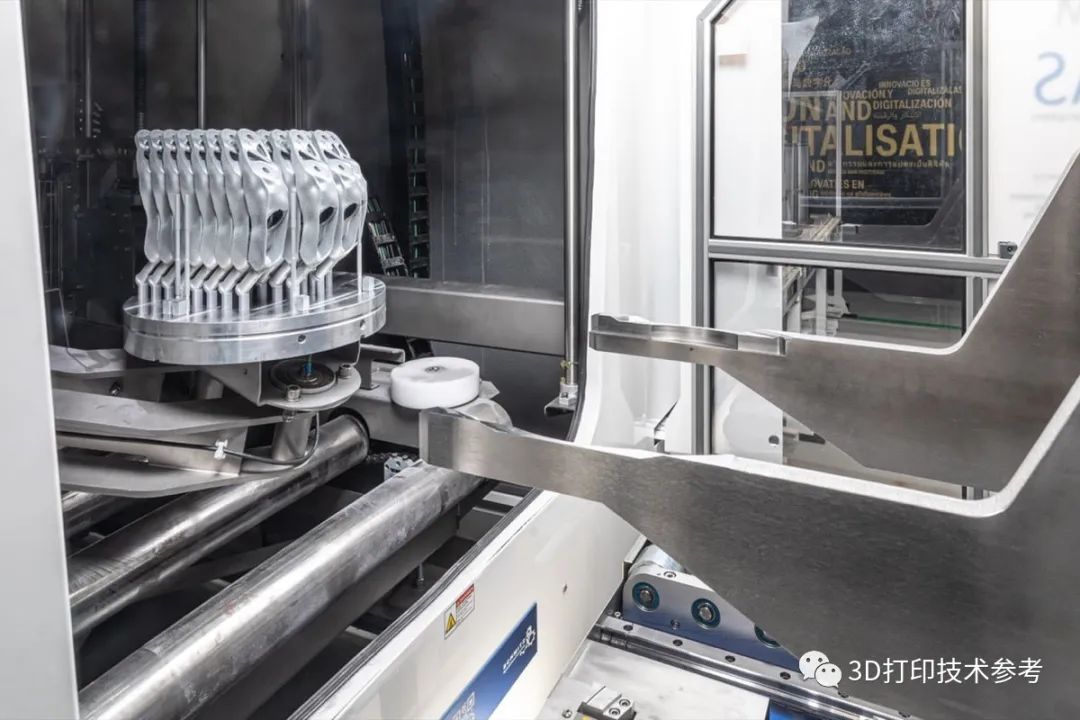
在IDAM项目实施期间,开发了自动生成3D打印数据的新概念。全自动模块将使用过后的旧金属粉末运送到加工站,在那里进行独立处理。部件的后处理在专门设计的工作站中进行,这些工作站也是全自动的。组件的质量是重中之重,IDAM通过使用传感器在线监控3D打印过程来保证零件质量,使用CMOS相机和高温温度计检查来自熔池的排放物质,此外,还使用AI算法将记录的数据与实际组件质量相关联。
除聚合物3D打印自动化产线成功实施外,3D打印技术参考还注意到,宝马集团最近展示了一条砂型3D打印的自动化产线。
Voxeljet创始人兼首席执行官表示,“宝马兰茨胡特工厂的全自动3D打印生产线不仅是Voxeljet的一个重要里程碑,也是整个3D打印和汽车行业的一个重要里程碑。我们相信,这种定制的、接近零排放的解决方案将成为行业标准。”
END
3D打印自动化产线项目无疑将会给增材制造技术的工业化规模实施带来巨大改变,同时促进效率及成本效益的进一步提升。一旦减少了人工参与,3D打印厂房将真正变成了黑灯工厂,各环节的自动化运行将使人们看到3D打印将真正成为革新制造技术的重要推手。
宝马集团作为汽车行业的头部企业,成功实施覆盖几乎所有类型3D打印技术的生产线,势必推动该行业实施增材制造技术的规模,并引领其他行业加大实施的力度。
主编微信:2396747576(请注明身份); 硕博千人交流Q群:248112776;网址:www.amreference.com
延伸阅读:
2.特斯拉正与多家3D打印砂型铸造公司合作——电动汽车更便宜的关键