德国宇航中心在零重力条件下测试金属粉末床熔融工艺(天问一号携100余件3D打印产品)

德国宇航中心(DLR)自2017年就已开始测试零重力条件下的金属粉末床熔融增材制造系统,按照计划,该系统在经过一系列的试验和测试后,会被设计为火箭的有效载荷,并将在本年度首次由MAPHEUS火箭发射升空。
DLR研究项目的主题是粉末床激光烧结/熔融(SLS/SLM)工艺,该工艺仍然是使用聚焦激光束通过层层熔化粉末实现零件成型。与地面相比,零重力条件下的工艺探索要复杂的多。
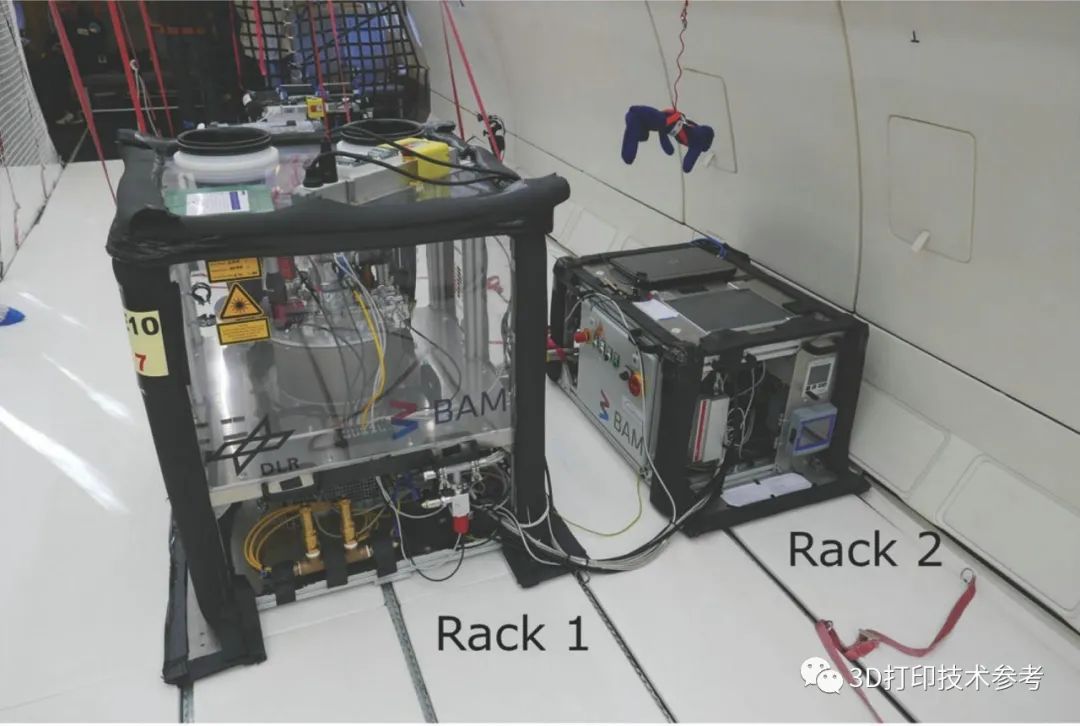
对金属粉末的有效处理,是在降低重力甚至完全失重的情况下面临的最大挑战。有针对性地实现厚度均匀的致密粉末层非常重要,它是影响最终部件质量和材料性能的关键因素。此外,粉末层还必须在打印床上保持稳定,直到完成打印。为了实现这一目标,研究人员开发了一种空气气体流动吸入系统,在没有重力的情况下,粉末被有效地“吸”附在打印床上。这种在整个压力范围内稳定粉末的方法已经在之前的抛物线形飞行中进行了多种测试,并且显示出很高的可靠性。
金属粉末床熔融工艺与空气气体流动吸入系统原理
这个用于稳定粉末的气流装置相对于整个增材制造系统来说具备独立的电源供应,重量很轻,且完全自动化运行。其强度和稳定性能够承受火箭发射期间产生的载荷。整个3D打印过程可以从地面通过遥测连接进行监控,火箭有效载荷和地面站将在抛物线飞行过程中并行工作。除了首次在失重状态下对硬件进行测试外,该实验还将针对不同材料和要求更高的材料(如固态金属玻璃)进行系统的参数优化。
微重力下打印的金属扳手
开展微重力条件下的3D打印研究,是当今包括欧洲航天局、NASA、俄罗斯和中国在内的众多航天机构的热门话题。
NASA未来从国际空间站迈向小行星及火星的太空制造技术规划
中国微重力3D打印实验历程
中国在今年5月发射的新一代载人飞船试验船上进行了多种类型的太空3D打印实验,包括碳纤维复合材料3D打印以及金属/陶瓷立体光刻微米级精度3D打印。为了实现这一目标,以中科院为代表的中国研究团队早在2015年就开始了微重力状态下的3D打印实验。
2016年3月,中科院团队利用抛物线飞机产生的微(低)重力环境成功开展了微重力高分子材料及其碳纤维复合材料增材制造技术验证,使我国成为继美国之后国际上第二个实现了这类材料的微重力快速成型相关技术试验验证的国家。
2018年6月,中科院团队利用抛物线飞机开展了低重力金属熔融铸造技术的研究,成功实现了模拟在微重力、月球重力(1/6g)以及火星重力(1/3g)条件下的金属零部件的制造。该技术试验共制造了8件金属样品,样品表面平整,证明制造过程与相应使用的材料对于不同重力条件适应性良好。
抛物线模拟微重力原理
不同重力条件下金属铸造实验用增材制造的陶瓷模具(a)和铸造的金属零部件(b)
同期,中科院团队还将精细陶瓷粉末与有机树脂混合,通过调控流变特性得到了可在微重力环境下有效约束精细粉末的软物质材料。随后利用抛物线飞机开展了微重力制造试验,在国际上首次开展了微重力环境下陶瓷材料的立体光刻成型技术实验。
陶瓷浆料的立体光刻技术试验装置(a)及样品(b)
以零重力条件下的立体光刻技术为例,国际同行普遍认为该工艺在微重力环境下不太可能被使用,因为其主要原材料是液体,而液体在微重力环境中非常容易自由飘散。因此,该实验的难点就在于需要攻克液体在失重环境下难以精确控制的问题。
2020年5月,该实验装置第一次在载人飞船试验船上进行轨精细成型实验任务,最终通过立体光刻3D打印,成功精细制造出微缩版的国旗、中科院院徽、中国载人航天工程标识、三维支架等8件样品,成功实现在失重环境中陶瓷/金属软物质材料的微米级精密在轨制造。
END
增材制造为从液体、粉末或细丝状材料制造组件提供了广泛的选择,包括金属、塑料和陶瓷以及复合材料在内的几乎所有材料都可以3D打印,越来越多的材料已被市场成熟使用。然而太空完全是不一样的情景,所使用的设备硬件和材料有根本不同的要求,而且会更加复杂,即便研究人员已经为失重环境下的制造过程进行了充分的试验准备,但也可能面临多种多样的风险。
虽如此,太空3D打印依旧具有巨大吸引力。随着信息、材料、自动化、快速成型等技术的高速发展, 特别是增材制造技术的进步, 使太空制造技术取得突破性进展。未来太空制造技术将趋向于更高精度、更大尺度以及更快速度,3D打印将发挥重要作用。
联系微信:2396747576; 硕博交流和资料下载群:867355738;网址:www.amreference.com
1.专访中科院太空制造技术团队:介绍太空立体光刻3D打印的意义