[置顶]工艺综述:金属增材制造技术的重要创新发展及代表性企业

在这一切正在发生的同时,一些新工艺似乎也在以更为颠覆性的方式革新我们所认知的3D打印技术。例如,所谓的区域金属3D打印正在突破激光逐点扫描的对速度的限制,无支撑金属3D打印则进一步突破了对设计复杂性的限制;材料喷射和基于光刻的金属3D打印工艺在超精密零件生产方面有特殊优势;粘结剂喷射工艺则将金属3D打印提升到批量制造的水平;由冷喷涂、搅拌摩擦焊以及超声波焊接发展起来的新3D打印形式在多材料、大尺寸零件制造方面充满潜力。
大量金属增材制造新技术、新工艺正在不断地开发出来,这使得金属增材制造市场呈现出日益多样化、生机盎然的景象。本期,3D打印技术参考着重介绍这些新的工艺形式,其中很多种国内尚未有研究进展。
传统激光粉末床熔融技术的新发展
所有金属增材制造技术中,PBF的工业化应用研究最多,工艺的标准化和成熟度也最高。经过近十年的增材制造服务商的代工生产,PBF技术已经证明了其可以使用最多种类的金属合金。今天金属PBF技术虽然已经实现了高度的自动化,但是仍然存在许多挑战:一是新建PBF增材制造生产线需要很高资本投入;二是金属增材制造零件的质量保证和过程有效监控还缺乏有效手段;三是可用的金属粉末原材料成本还比较高,成形件支撑结构的去除和表面抛光等后处理过程费时且难以实现自动化。
除了金属PBF技术的传统领导者,如EOS、SLM Solutions、3D Systems和GE Additive,目前还有一些初创公司正在不断开发新的、有效的金属PBF工艺,如荷兰Additive Industries开发了一种多工位模块化集成的PBF激光增材制造设备,提高了自动化程度。
作为粉末床金属3D打印工艺的重要形式,面区域金属3D打印与无支撑金属3D打印备受瞩目。
面区域金属3D打印通过光学设计,将200多万个激光点融合为一束激光,每个激光点的能量均可以通过切片图像的像素设计控制能量,一次可以实现2×2mm甚至15×15mm的区域曝光熔化,此举大大提高了成型效率。该技术的代表企业为美国Seurat公司,据3D打印技术参考了解,国内某知名金属3D打印制造商也在开发工艺。
而无支撑金属3D打印,通过非接触送粉、变化的能量输入以及实时反馈机制实现了相比传统SLM技术更大倾角的无支撑打印。该突破对于制造更为复杂结构的零件至关重要,因此尤其被航空航天制造商所看重。该技术的代表企业为美国Velo3D公司,国内尚无公司进行对标技术的开发。
作为粉末床金属3D打印技术的另一条赛道,增减材技术的发展似乎并未达到预期中的革命性发展。Matsuura和Hermle两家公司此前推出了增减材一体的PBF激光增材制造设备。
有热源制造大尺寸、多材料零件的金属3D打印工艺
DED金属增材制造技术是使用激光束、电子束、电弧等能量源熔融金属粉末或线材,逐层制造、累积成形的一类技术(LENS、EBAM、WAAM)。这类DED技术通常还需使用CNC对成形件进行切削加工,以获得具有较好精度的最终零件。
这种增减材复合工艺比单纯的CNC或金属3D打印成形效率要高很多。除了成形效率方面的优势外,最重要的是这些增减材复合工艺还能制造长度可达几米的超大型金属承力结构零件。DED金属增材制造技术与成熟的数控机床系统相结合,能够通过整合工艺流程,大大提高制造自动化程度和生产效率。
多种增材工艺结合以及将增材工艺与传统制造工艺结合,制造出多材料部件,已经成为这些手段的重要应用形式。NASA已经采用选区激光熔化、DED并配合CNC技术制造了铜-镍复合的双金属材料燃烧室。
从事该工艺的企业主要分为两大类:一类是采用增减材复合制造的传统的高端机床制造商,另一类是开发新的DED技术的初创公司。DMG Mori、TRUMPF和Mazak是从事该技术开发传统制造代表企业。另一方面,Sciaky、BeAM和Optomec则是首批开发和应用DED技术的增材制造公司,Sciaky是唯一一家使用电子束焊接进行金属增材制造的公司,Norsk Titanium在该领域已经取得了重要成就。
无热源制造大尺寸、多材料零件的金属3D打印工艺
此类技术中最早开发出来的是超声波焊接增材技术,它使用金属箔材料,工件在一定的压力下将弹性体振动能量转变了工件间的摩擦功、形变能以及有限的热能,从而在不发生熔化的状态下实现箔材料间的冶金结合。金属超声波焊接增材技术的优点是能够适用于各种金属材料的焊接增材、且焊接过程无高温污染、无损伤缺陷等,但是由于焊接功率随着箔材厚度增加将呈指数级剧增,因此主要用于丝、箔以及小型零件。
搅拌摩擦增材制造的基础是搅拌摩擦焊技术,它利用搅拌针与连接件的搅拌摩擦产生热量软化连接处的材料,再通过轴向的压力使得材料连接在一起。这样的焊接方式没有经过金属的熔化与凝固,只是经过塑性软化和轴向的挤压,连接处在材料性能上存在一定的优势。
喷射沉积固结(冷喷涂)也是金属固结增材制造技术技术中较常见的一种,它将金属粉末以超音速喷射、沉积在基材表面,从而实现逐层制造。这种方法的关键优势在于能够快速、较低成本地生产大型金属零件,且可使用非球形粉末,制造多材料金属零件。
目前世界上开发实用的超声波焊接和摩擦焊接增材制造技术只有两家外国公司。Fabrisonic公司的UAM技术(超声波增材制造)主要应用航空航天,该公司的部分资金来自美国宇航局喷气推进实验室(JPL)。MELD是一家具备摩擦焊接增材制造技术的制造性企业,能够提供增材制造服务或摩擦焊接增材制造设备。喷射沉积固结技术,可能是目前冷固结工艺中应用最广泛的工艺,它最初是由两家澳大利亚公司SPEE3D和Titomic推出,前者专注于铜和铝等材料,而后者几乎完全专注于钛及钛合金。最近德国Hermle、美国GE Additive也都在内部开发冷喷涂增材制造制造系统。
基于烧结的粘结剂喷射、挤出及光固化金属3D打印工艺
依赖于烧结成形的金属3D打印技术已经成为金属增材制造技术一个重要门类,它使用聚合物材料将金属颗粒粘合在一起、然后再烧结成形最终部件。在具体的工艺形式方面,包括粘结剂喷射以及将掺有金属颗粒的丝材挤出和浆料光固化的工艺。
粘结剂喷射工艺,被认为是一种最有可能的规模化、数字化、低成本的金属增材制造技术。该公司所使用的的材料可选择传统注射成型的金属粉末,相比基于激光的粉末成本更低,以面成型的工艺特点极大提高了打印效率,初始无热源的成型方式使其在复杂零件制造方面也显优势。但该技术未获得广泛应用的主要问题是零件质量,特别是与最终应用相关的后烧结变形、开裂以及力学性能,在面临最终应用时存在挑战。
在金属粘结剂喷射技术领域,ExOne是唯一取得较大规模商业化应用的金属增材制造公司。虽然ExOne是该技术的早期领导者,但该技术的规模化应用最近才开始显现,如今ExOne已被Desktop Metal高调收购,引领了该技术的快速发展。惠普(HP)和通用电气(GE)这些国际大型公司也在前几年前进入了该领域,并在批量化、规模化应用方面取得了较大进展。
采用材料挤出和光固化成形技术的增材制造公司也能使用低成本的丝材或浆料来制造金属零件,国际化工巨头BASF因此开发了适用于该工艺的金属丝材。金属材料挤出工艺适合于制造工装、夹具以及零件原型,目前已在汽车领域获得应用。从事该技术的知名公司有Desktop Metal以及国内的Raise3D、纵维立方等。
基于光固化的金属3D打印,根据光聚合原理生产高精度零件生坯,其原料为金属粉末和光敏聚合物的混合体。通过掩模曝光,可以精确快速地成型整个层面,聚合物粘结剂选择性的在局部交联,将金属粉末粘结在一起。打印完的生坯经历脱脂和烧结后可以形成致密化的零件。这种制造方式特别适合小尺寸金属零件的3D打印,并能实现从医疗到汽车、航空航天到奢侈珠宝等广泛应用的复杂零件的精确、高质量生产。目前,从事该技术的公司主要有MetShape和Incus。
金属材料喷射技术(MJ)
一般来说,材料喷射技术被认为是精度最高、技术最成熟的增材制造技术,这是因为它采用了传统的喷墨打印技术、从而能够精确控制成千上万的数字控制喷嘴来喷射材料。然而,在金属增材制造领域中,材料喷射是一个原材料种类非常有限的增材制造工艺,因为喷射使用的液态金属难以制备。
尽管如此,这一细分市场仍是创新和技术突破最可行的领域,因此我们将其作为一个独立的金属增材制造技术来对待。目前可用于金属材料喷射技术的材料只有两大类:一种是已经商业化的、利用金属纳米颗粒与液体混合形成的纳米墨水;另一种是正在研发的、使用电磁场驱动喷射的熔融液态铝。
虽然许多金属粘结剂喷射公司也宣称自己能够使用纳米金属墨水打印金属零件,但唯一能够真正开发纳米金属墨水并实际应用的公司目前仍只有Xjet,其使用材料喷射技术来制造陶瓷和金属零件,如钢和银。遗憾的是,该工艺推出了多年,但在商业化和应用方面,似乎一直未有太多起色。
与Xjet材料喷射工艺类似的,中国梦之墨公司推出的液态金属3D打印机专注于电子电路打印,并取得了一定的成绩。除此工艺形式之外,施乐公司收购了一家发明了使用熔融铝线制造金属零件的初创公司,其每秒可喷射1000个液滴,用于零件的堆积制造,这也是目前使用材料喷射技术高效率、低成本制造金属零件的可用解决方案。
END
金属3D打印技术经过几十年的发展,制造局限获得了极大突破,制造形式更加丰富多样,制造效率也大为提升。尤其值得注意的是,本文所提到的绝大多数工艺形式是金属3D打印技术的新发展,国内在很多方面有的还未涉足、有的则仍处于研究阶段。在新技术发展领域,以美企等为代表的国外先进制造商具有领先优势。
3D打印技术与国内的发达的传统制造技术相比,在很多领域可能并不具备成本优势,但作为一项重要的未来生产力,技术储备不可或缺。我们期待,国家能有重大的科技专项能扶持新技术的发展,让先进技术在未来重要的领域发挥作用。
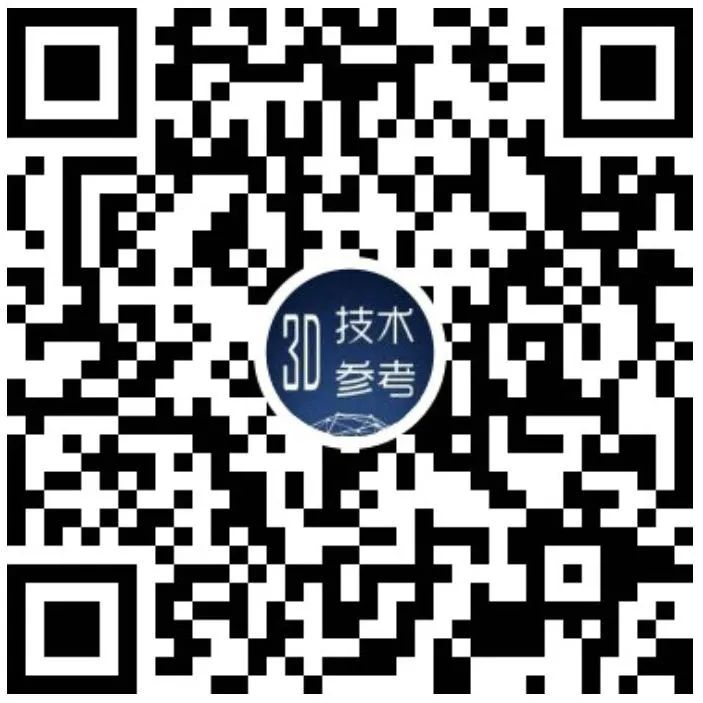
视频号
了解最新技术应用
主编微信:2396747576;硕博千人交流Q群:867355738;网址:www.amreference.com
延伸阅读:
2.王华明院士《科创中国》演讲视频:3D打印,重大装备制造业的新机会
3.深蓝航天3D打印整机制造火箭发动机搭载试验箭完成「公里级起降回收」
4.视频:国家增材院10米超大型铝合金火箭连接环3D打印制造技术