
高性能航空航天飞行器正朝着速度更快、寿命更长、稳定性更高的方向发展要求其发动机推重比和效率不断提升,热防护系统耐热性和服役可靠性增加。随着航空发动机推重比和热效率的提高,发动机的涡轮进口温度需不断提高。开发具有优异高温力学性能和更高耐热极限的新型轻质超高温结构材料已成为发展更高推重比航空发动机的迫切需求。
基于熔体生长技术制备的氧化物共晶陶瓷具有高熔点(>1700℃)、低密度(<6g/cm3)、天然的抗氧化性和极为突出的高温力学性能,具有可应用于航空航天领域的巨大潜力。熔体生长的Al2O3/GAP共晶陶瓷弯曲强度可由室温保持到1700ºC,在该温度下热暴露500h后,强度基本保持不变,表现出优异的性能稳定性。1700ºC的大气氛围中热暴露500h后,氧化物共晶陶瓷的尺寸、重量、表面粗糙度基本不变,体现出杰出的抗氧化性和抗热腐蚀性。氧化物共晶陶瓷在1700ºC下水蒸气环境中保持10h后,质量没有损失,强度没有下降,表现出优异的抗水氧腐蚀性能,ZrO2的添加能够在共晶陶瓷中发挥相变增韧作用。
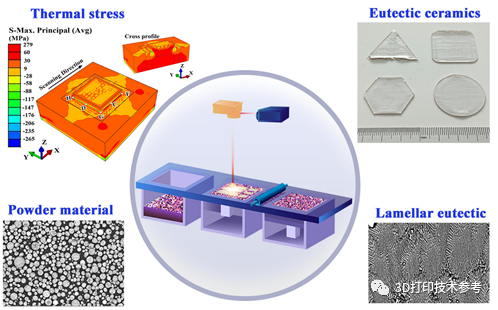
图1 激光粉末床熔融技术结合有限元数值模拟制备Al2O3/GdAlO3/ZrO2氧化物共晶陶瓷及其试样和组织形貌
激光粉末层熔融技术以高能激光束作为热源,按照设定的三维模型,经逐层加工/层层堆积制备三维实体样件。同传统制备方法相比,该技术摆脱了坩埚、夹具等装置的限制,具有柔性制造、近净成形、生产周期短、成本低等特点,被誉为是制造领域的一场“绿色工业革命”。该技术在制备复杂结构零件方面具有无与伦比的优势。将激光粉末层熔融技术可加工复杂构件的突出优势应用到氧化物共晶陶瓷的制备中,有望突破氧化物共晶陶瓷的一步近净成形,对于推动我国航空航天用新型轻质、高强、耐高温、抗氧化、长寿命超高温结构材料的发展具有重要战略意义。
近日,西北工业大学苏海军教授团队报道了一种通过激光粉末床熔融技术制备复杂结构氧化物共晶陶瓷的新方法。利用热力耦合数值模拟方法分析研究激光逐层打印氧化物共晶陶瓷过程中的温度场和应力场,进一步分析氧化物共晶陶瓷中裂纹的形成及扩展机理。结合数值模拟结果及实验优化,制备获得了尺寸约为30mm×30mm×1mm,表面光滑且具有典型复杂结构特征(圆形、三角形、正方形、六边形)的Al2O3/GdAlO3/ZrO2氧化物共晶陶瓷试样,如图1所示。直接快速凝固获得的三元共晶陶瓷材料具有超细层片状组织特征,共晶间距可细化至88nm。相关工作以题为“Large-size complex-structure ternary eutectic ceramic fabricated using laser powder bed fusion assisted with finite element analysis”的研究论文发表在Additive Manufacturing,2023, 75: 103627。
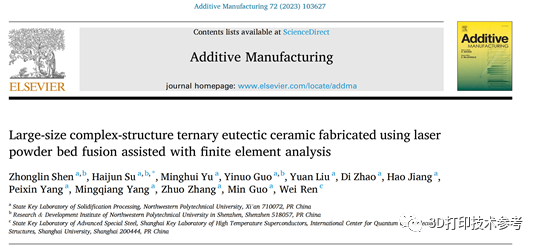
https://doi.org/10.1016/j.addma.2023.103627
激光粉末床熔融技术,利用高能激光束按照设定路径逐层快速熔化、凝固粉末材料。粉末材料经历急热、急冷、层层熔凝的加工方式,成形过程涉及温度场、应力场、流场等多场耦合,熔池经历复杂的非平衡态快速凝固过程,温度变化剧烈,冷却速率快,影响因素众多,因此成形极易产生开裂、翘曲、熔化不良等多种宏微观缺陷。严重降低试样性能,且极易导致成形失败。氧化物共晶陶瓷材料脆性大,硬度高,熔点高,裂纹缺陷抑制难度大,激光增材制造工艺窗口小。因此,探明合适的打印窗口并抑制缺陷的产生以提高打印成功率并改善试样性能是激光增材制造的关键难点。
随着计算机技术的飞速发展,借助有限元数值模拟技术能够辅助获得优化工艺窗口,并且对于深入了解加工过程,获得激光熔覆过程中的温度场及应力场分布特征,进一步揭示缺陷及组织形成及演变机理具有重要的指导意义。
为获得熔体生长的氧化物共晶陶瓷,薄层的具有共晶配比的陶瓷粉末材料经过高能激光器扫描下,快速并完全熔化,自生复合,层层熔覆成形共晶氧化物陶瓷。制备实验采用自主设计研发的氧化物陶瓷LPBF装备。粉末材料为喷雾造粒法制备的具有三元共晶配比的陶瓷粉末。粉末材料呈球形或近球形,粉末粒度D50=28.3μm。激光扫描策略为“之”字形,层间旋转90°的扫描方式。激光功率200-300W, 扫描速率100-450mm/s。高能激光器快速扫描下,陶瓷粉末材料能够完全熔化,自生复合,层层堆积成形三元共晶氧化物陶瓷。
利用ABAQUS软件建立单道、单层、多道、多层加工过程中的热力耦合模型。利用单道扫描实验获得的共晶陶瓷熔池形貌,验证温度场结果的有效性。通过顺序耦合数值模拟获得应力场分布,利用XRD德拜环应力测试验证应力模拟结果。
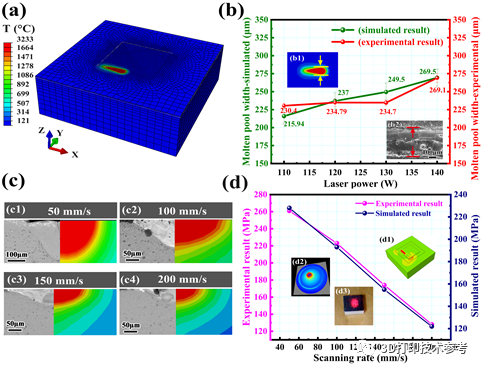
图2 热力耦合数值模拟及其验证工作:(a) 温度场模型, (b) 利用熔池形貌验证不同激光功率及扫描速率(c)下的温度场模拟结果, (d) 利用XRD德拜环应力测试验证热应力模拟的有效性
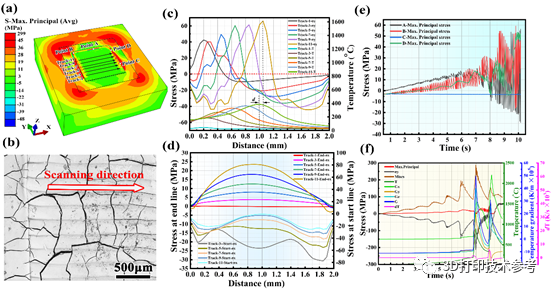
图3 多道LPBF应力场分布特征(a),多道试样表面裂纹分布(b),不同加工道次下试样边缘应力及温度分布特征(c-d),不同节点处的应力及温度分布(e-f)
综合比较不同位置处的最大主应力特征发现裂纹敏感性较高的区域为熔覆层边缘沿扫描熔覆道方向的中心位置。随熔覆层数的增加,最大主应力逐渐从拉应力转变为压应力,Y轴向(垂直于扫描方向)拉应力较大。因此,多道堆积过程中沿扫描方向的纵向裂纹敏感性较大。沉积方向的应力表现为压应力,随层数的增加应力值逐渐增大。加工过程存在一定幅值的切应力,该切应力是导致裂纹偏转的主要原因。
随扫描道数的增加,平行于扫描方向的Y轴主应力逐渐增加,且最大主应力位置与最大温度值所在位置有半个熔池距离的偏移量,垂直于扫描方向的X轴向主应力随扫描道增加逐渐增大,扫描起始位置处则为压应力。随扫描道数量增加,应力幅值逐渐增大,因此,为限定最大应力幅值,可以适当减小单道扫描长度,扫描长度过小则由于激光初始阶段不稳定及激光高温热震作用极易产生缺陷。对脆性材料,实验过程中重点控制拉应力幅值,抑制裂纹缺陷是保证熔覆过程稳定持续的关键。