主流3D打印工艺制备SiC陶瓷的优缺点及国产方案带来的新突破
导读:近日,中国科学院上海硅酸盐研究所陈健副研究员首次提出高温熔融沉积3D打印结合反应烧结制备高固含量SiC陶瓷的新方法,成功制备出力学性能接近于传统方法制备反应烧结的SiC陶瓷。相关研究成果发表在《Additive Manufacturing》,并申请中国发明专利2项。
碳化硅陶瓷的应用与传统制造难点
碳化硅陶瓷的广泛应用
目前对各种复杂结构形状SiC陶瓷需求急剧增加,传统的制造方法复杂、耗时、模具设计制作周期长。由于其极高的硬度和脆性,导致其加工极其困难。刀具不仅磨损严重,而且还可能产生裂纹等缺陷,难以达到良好的表面质量和尺寸精度。基于以上缺点,结合3D打印技术的SiC陶瓷制备技术成为目前研究和应用的主要发展方向,能良好地解决传统陶瓷材料复杂形状难成型、难加工,制作周期长、成本高的问题。
主流3D打印工艺制造SiC陶瓷的不足
当前,3D打印工艺制造陶瓷的技术种类主要包括SLS (激光粉末烧结)、DIW(直接墨水书写)、SLA (光固化)、和BJ (粘结剂喷射)以及FDM(熔融挤出),上海硅酸盐所的科研人员对这几种的陶瓷3D打印技术进行了测试与认证。
与金属3D打印不同的是,陶瓷材料不能通过激光加热陶瓷粉末直接打印。直接SLS制件在烧结过程中产生的热应力难以避免产生裂纹,导致最终产品力学性能较差。
直接墨水书写(DIW)技术是将陶瓷粉末与各种有机物混合,制成陶瓷墨水,然后通过打印机将其打印到成形平面上形成陶瓷坯体。目前,该技术的难点是墨水中的固相含量太低,这会导致陶瓷坯体致密度较低。
采用直接墨水书写技术3D打印的Al2O3坯体
SLA是一种基于光敏陶瓷浆料光聚合的有效紫外光固化技术,是当前主流的陶瓷3D打印工艺,但由于碳化硅的高吸光度、高折射率,限制了浆料的固化厚度、固含量等参数。
粉体熔融沉积成型(FDM)3D打印技术在传统熔融沉积方法的基础上,采用粉体混炼然后挤出机构3D打印制备SiC陶瓷,该方法具有以下优点:可粉体打印,原料制备方便;在常温状态下,粘接剂粘结力强;在高温状态下,粘接剂流动性好;在打印过程中可以通过温控消除应力;打印样品在常温下强度大;打印产品可常压烧结制备或反应烧结制备SiC陶瓷;打印料可循环利用。
BJ工艺可以快速打印复杂形状,同时保持打印精度。然而,BJ工艺限制了粉末的填充密度,导致SiC体积分数受限。
NASA格伦研究中心采用粘结剂喷射技术打印的SiC陶瓷复合材料涡轮发动机部件
研究团队对比发现,常规的3D打印方法制备陶瓷材料,往往有机物含量较高,有利于打印成型,而陶瓷固含量相对较低,采用常压烧结方法一般材料难以达到高致密度,而SiC反应烧结是通过浸渗的熔融硅与坯体内的碳反应,将坯体中的SiC颗粒结合起来,从而实现陶瓷致密化。相比于常压烧结和热压烧结等常规方法,更容易实现材料致密化,同时反应烧结具有烧结温度低、烧结前后尺寸变化小等特点。
国产3D打印方案为高固相含量SiC陶瓷打印带来可能
如能实现SiC陶瓷大尺寸、轻量化、一体化制造显然是更好的选择。作为国内领先的金属/陶瓷挤出3D打印工艺的制造商——升华三维给出了解决方案——大尺寸独立双喷嘴打印机UPS-556系统。
PEP技术是3D打印+粉末冶金”相结合的金属/陶瓷间接3D打印技术,是Powder Extrusion printing的简称。研究团队使用PEP技术实现了高固含量SiC陶瓷材料的3D打印,结合反应烧结制备出致密高强的SiC陶瓷材料,从而解决SiC陶瓷材料复杂形状难加工,制作周期长的问题。
利用UPS-556系统,PEP技术将热加工过程转移到烧结步骤,这使得更容易管理热应力,因烧结温度低于其他类型的直接3D打印工艺中所需的完全熔化温度,并且热量可以更均匀地施加,从而确保了产品性能的一致性。
UPS-556采用独立双喷嘴设计,可以同时打印或者各自轮流打印金属和陶瓷不同种类材料的复合产品开发,实现复杂结构和产品的快速成形,大大节省了产品打印时间,具有操作简单、工业型、高精度、高质量、高性价比等优点。再结合反应烧结制备工艺在复杂结构碳化硅陶瓷产品近净尺寸成型方面形成了巨大优势,从而提高了产品生产效率并降低生产成本,为制造复杂结构陶瓷提供了新的工艺方案。
SiC陶瓷3D打印示意图
近日,该研究团队首次提出了高温熔融沉积结合反应烧结制备SiC陶瓷新方法。该方法采用高温原位界面修饰粉体,低温应力缓释制备出高塑性打印体,获得了低熔点高沸点的高塑性打印体,材料固含量超过60vol%;之后对塑性体进行高密度叠层打印,打印的陶瓷样品脱脂后等效碳密度可精确调控至0.80 g·cm-3,同时对陶瓷打印路径进行拓扑优化设计,可在样品中形成树形多级孔道;最终陶瓷样品无需CVI或PIP处理直接反应渗硅烧结后实现了低残硅/碳的高效渗透和材料致密化,SiC陶瓷密度可达3.05±0.02 g·cm-3,三点抗弯强度为310.41±39.32 MPa,弹性模量为346.35±22.80 GPa,陶瓷力学性能接近于传统方法制备反应烧结SiC陶瓷。
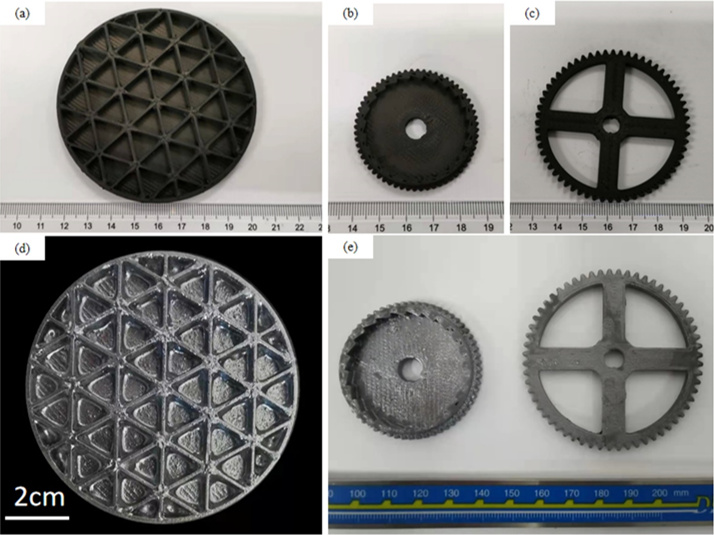
不同形状尺寸的SiC陶瓷
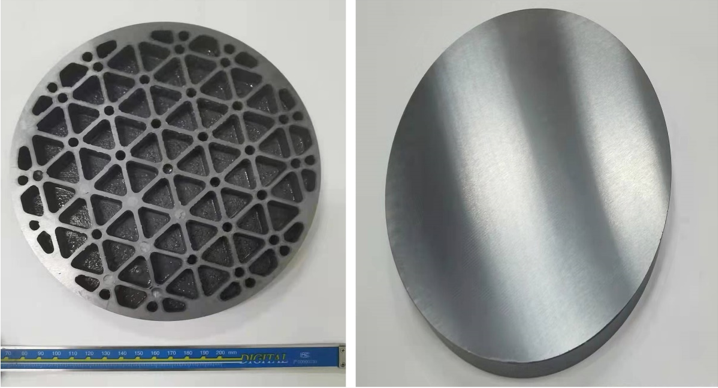
相关研究成果发表在《Additive Manufacturing》,并申请中国发明专利2项。该方法有望实现低成本、高效率的复杂结构陶瓷产品近净尺寸成型技术的工业化应用。同时该塑性体打印方法避免了微重力条件下粉体打印潜在的危害,为未来空间3D打印提供了可能。
主编微信:2396747576;硕博千人交流Q群:867355738;网址:www.amreference.com
延伸阅读:
1.上百家3D打印企业!9月14-16日Formnext展览会解锁增材智造新技能!
2.几种主流陶瓷3D打印工艺的关键特点及航空航天应用面临的挑战
4.国家增材中心《大讲堂》第一讲:陶瓷增材制造控形控性关键技术