干货分享:间接陶瓷增材制造裂纹的形态、产生原因及应对策略
造成陶瓷增材制造工业应用滞后的主要原因是成形缺陷过多和成形质量差。其中,裂纹缺陷严重影响陶瓷件的力学性能,是该技术向工业实用化推进的最大障碍。目前,现有的陶瓷增材制造裂纹缺陷研究主要集中在实验方法的裂纹形貌和抑制上。在往期文章中,3D打印技术参考已经介绍了间接和直接陶瓷增材制造的裂纹形态,本期内容主要介绍陶瓷间接增材制造裂纹的形成机制,探究裂纹形成机理。
1. 陶瓷间接增材制造裂纹产生的机制
根据裂纹形成阶段,间接陶瓷增材制造中的裂纹缺陷分为成型裂纹和烧结裂纹。成型裂纹主要是由于生坯成型阶段收缩应力超过聚合物结合强度造成的,形貌表现为水平和十字形裂纹,尺寸为纳米到微米量级。烧结裂纹出现在高温热处理阶段,裂缝开口大,方向性不明显,横向、纵向和斜向裂纹在烧结件表面交联分布,严重影响陶瓷件的力学性能。
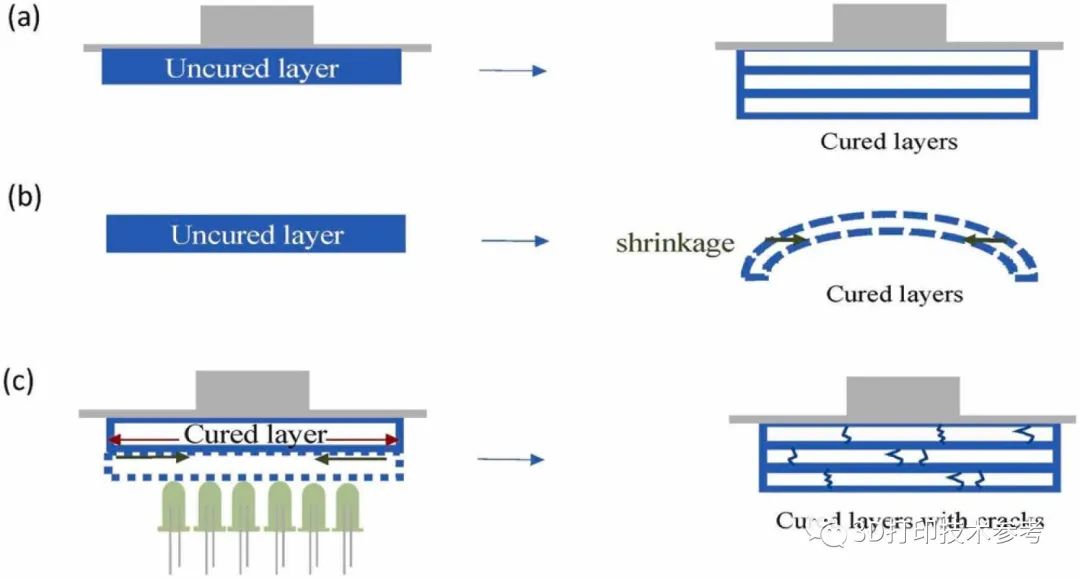
在高温脱脂热处理过程中最容易出现裂纹,由于生坯中含有大量的有机结合剂,高温热处理过程中有机结合剂的快速热解导致局部压应力过大。在局部压应力下,陶瓷粉末之间的毛细力,液相粘合剂被有机物热解产生的气体混合物从生坯内部带到表面。在粘结剂排出过程中,生坯内部容易形成交联孔隙。孔隙受到高温热膨胀,产生高内压应力,导致它们破裂并形成微裂纹。此外,在极端升温速率下,当陶瓷材料的结合强度超过生坯内局部区域气体聚集产生的压应力时,会导致零件开裂形成宏观裂纹。陶瓷坯体中可能存在未反应的单体和光引发剂,固化层末端未反应的光引发剂在高温下热解产生自由基,使残留单体聚合,产生较大的机械应变并且增加了样品中的残余应力,进而破坏了聚合物的键合关系,导致生坯出现更严重的宏观裂纹。
脱脂过程中气体释放过程与陶瓷件裂纹分布
SLS技术通过激光束直接熔化低熔点粘结剂粉末。由于坯体制备阶段激光能量密度低,激光烧结冷却慢的特点,坯体温度梯度低,不易产生裂纹缺陷。裂纹多形成于高温脱脂、烧结和冷却阶段。在高温脱脂阶段(400~600℃),粘结剂迅速热解,固相陶瓷颗粒原子发生迁移,陶瓷颗粒接触点通过形核和晶粒长大逐渐形成烧结颈。粘结剂热解导致陶瓷生坯严重体积收缩,导致烧结颈部内原子键的结合强度或晶界界面能被局部区域收缩应力超过,导致严重的收缩裂纹。在高温烧结阶段(1600℃以下),陶瓷颗粒充分烧结并熔合在一起,随着烧结温度的升高,晶粒尺寸变得过于粗大。晶粒粗大导致晶界结合强度低,在后续冷却收缩引起的收缩拉应力作用下,易沿晶界形成微裂纹缺陷。除了晶间裂纹,热收缩产生的拉应力也会在层间结合强度低的地方产生裂纹缺陷。此外,烧结阶段的极端加热速率导致烧结部件表面和内部之间的温度梯度过大,由此产生的热应力会导致生坯出现开裂缺陷。烧结件在冷却阶段,其内部相变可能导致相体积发生变化,使大晶粒晶壳在静止的非晶核周围收缩产生微裂纹缺陷。
(a) 相变收缩微裂纹(b) 硅基陶瓷中微裂纹的形态
综上所述,陶瓷浆料间接增材制造裂纹主要发生在成型和烧结过程中,在成形阶段,收缩拉应力的存在是产生裂纹缺陷的关键因素,有机物热解产生的局部压应力是产生烧结裂纹的主要原因。陶瓷粉末铺粉间接增材制造裂纹主要发生在高温烧结过程中,局部拉应力引起的烧结颈断裂和晶粒过度长大引起的晶粒粗化是裂纹的主要来源。直接和间接陶瓷增材制造工艺在冷却过程中都会产生相变裂纹,这主要是因为相变过程伴随着相变粒子的体积变化,使相变粒子与基体之间产生拉应力和压应力造成的。
2. 间接陶瓷增材制造裂纹产生的抑制策略
裂纹缺陷严重阻碍了陶瓷增材制造技术的工程应用,是亟待解决的问题之一。从工艺、材料成分方面采取合理的裂纹抑制方法,有助于提高陶瓷件的成形质量。
-
优化工艺参数
对于间接陶瓷增材制造,激光功率、扫描间距和固化深度是成型工艺的主要参数。在随后的脱脂和烧结过程中,升温速率和保温时间都是可调参数。选择合适的激光功率可以避免生坯中出现大量未反应的单体,从而降低脱脂过程中出现裂纹的可能性。固化深度与激光功率正相关,合适的固化深度可以避免分层和层间水平裂纹。研究发现SLA制备Al 2 O 3,当层厚为50 µm时,适当增加固化深度可显著减少坯体表面裂纹数量。在随后的高温脱脂过程中有机物的缓慢热解可以有效减少或避免烧结部件中的开裂缺陷。通过降低陶瓷生坯中有机物的热解速率来避免烧结部件开裂,从而获得无裂纹陶瓷部件。合适的升温速率是保证有机物适当热解速率和获得无裂纹陶瓷件的关键;与升温速率相比,合适的保温时间有利于有机热解产物的稳定排出,避免因气体剧烈膨胀而产生的裂纹缺陷。此外,适当的烧结温度有助于降低生坯的热收缩率,从而减少烧结件的裂纹数量。足够的烧结温度和保温时间有利于晶体的熔化、生长和样品的高致密化,从而抑制裂纹的产生。
升温速率对裂纹的影响:在空气中(a) 0.1℃/min;(b) 0.5℃/分钟;(c) 1℃/分钟;(d) 3℃/分钟;(e) 5℃/min,在氩气中 (f) 0.1℃/min;(g) 0.5℃/分钟;(h) 1℃/分钟;(i) 3℃/分钟;(j) 5℃/分钟
总的来说,激光功率和扫描间距是制备近乎无裂纹生坯件的关键参数。在高温烧结过程中,生坯表面和内部受热不均引起的局部拉应力是裂纹萌生和扩展的主要原因。合理的升温速率和保温时间有效降低了烧结件的温度梯度,解决了因温度梯度引起的局部拉应力过大的问题。
- 调整材料成分
通过合理调整和优化材料成分,也可以获得高性能、无裂纹的陶瓷件。陶瓷浆料的成分对坯件的裂纹缺陷影响很大。通过在浆料中加入非反应性组分,可以减少固化层的聚合收缩反应,从而降低生坯内部的内应力。研究发现,通过向浆料中添加非反应性成分来改变聚合物基体的热脱脂工艺,从而最大限度地减少烧结部件的裂纹。
添加非活性成分对裂纹的抑制作用:(a,b,e)只含有活性成分;(c,d,f) 添加非反应性成分
浆料中陶瓷粉末的粒径大小也是影响坯体成型质量的重要因素之一,适当增加粉末的粒径可以显着减少成型裂纹的数量。研究发现,含有小粒径粉末的浆料在成型过程中会产生过度收缩变形,从而导致广泛的交叉裂纹,并且可以通过选择合适的粉末粒径来制备无裂纹的陶瓷部件。
不同粒径陶瓷颗粒抑制裂纹的效果:(a∼c) 0.35 µm;(d∼f) 3 µm;(g∼i) 7 µm
与基于浆料的增材制造技术相比,粉末扩散SLS技术中的裂纹也受材料成分的影响。在成型过程中,如果陶瓷粉末中的粘结剂含量不足,陶瓷颗粒就不能牢固地结合在一起,导致生坯出现分层和开裂缺陷。但粘结剂含量过高会导致脱脂烧结后生坯收缩变形较大,导致烧结件出现严重的宏观裂纹缺陷。因此,混合粉末中的粘结剂含量应尽可能低,同时不影响烧结件的密度和成形质量。
END
陶瓷增材制造尤其是间接成形技术已成为制造先进陶瓷的主要途径,但裂纹缺陷已成为限制其应用的主要障碍,也成为陶瓷增材制造技术最重要的研究方向和需要解决的关键问题。本文系统阐述了间接陶瓷增材制造裂纹的形态特征、产生原因和应对策略,为解决陶瓷增材制造裂纹产生具有指导意义。
本文内容素材来源:
主编微信:2396747576(请注明身份); 硕博千人交流Q群:248112776;网址:www.amreference.com
延伸阅读:
3.干货分享:陶瓷3D打印之粘结剂喷射技术的成形材料、优势与挑战
4.无需脱脂烧结,重点实验室采用高精密陶瓷FDM 3D打印研制介质天线