3D打印后处理 | 决定零件能否使用的最后关卡(全干货)
增材制造技术通过逐渐累加材料而非去除碎屑的方法制造零部件,因而与铣削、车削及火花电蚀等传统的材料切除工艺具有本质区别。从物品的三维CAD呈现出发,零件几乎可以说是“逐层叠加”到一组二维分层上。随后,这些分层在各自的顶部进行连续熔合,从而再现出三维物品。
通过增材制造技术,可以生产出传统制造技术无法实现的极其精确的几何形状零件,还能打印出具有集成功能特征的高度复杂的组件。通过增材制造,可以降低材料浪费率,有利于整体制造工艺。激光选区熔化 (SLM) 和激光金属熔覆 (LMD),是过去20年里达到工业规模的成熟水平的两种激光增材制造工艺。( 本文内容由DeburringTec去毛刺技术原创,已获得授权)
△ 广义增材制造的技术内涵与分类
△ 增材制造类型。根据硬件、材料要求和产品用途,增材制造可能包含多个工艺。图源:AUTODESK
采用3D打印制造的零件打印完从粉床中取来时,很少能直接做为最终产品使用,且低质量的表面可能会使其不适合某些工业用途。增材制造零件几乎无一例外都要经过磨削到精加工的后处理,以提高机械性能、精度以及表面质量。使用3D打印制作原型时这不是一个很大的问题,但随着技术向终端制造工艺过渡,规模化和自动化的后处理已成为建立增材制造生产线的关键瓶颈之一。
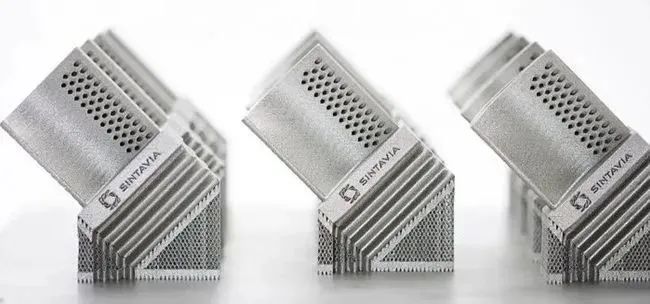
虽然改进金属粉末质量、优化成形方向和工艺参数能在一定程度上改善增材制造零件的表面质量,但是仍然无法完全解决增材制造零件表面粗糙的问题。这也是后处理所面临的共性挑战——表面质量。
从理论上讲,增材制造可以完全自由地创建复杂形状,但在实际生产过程中,对表面质量的要求往往需要对设计进行约束。如果需要进行表面加工,则对结构的限制就与过去一样;如果使用喷丸处理,则需要对薄和细长的结构进行限制。此外,表面质量问题还会导致应力集中,进而萌生裂纹,大大降低零件的抗疲劳性和断裂韧性,从而为零件的使用带来风险。另外,表面质量成本昂贵,可达到增材制造(AM)组件的60%,这无疑抑制了增材制造的研发热情。
△ 3D打印高性能植入性材料
目前增材制造主要的后处理方式包括光整加工和机械加工,如粉末清除、去应力退火、线切割、支撑去除、CNC、磨削、机械抛光、精加工以及热等静压等等。这些步骤中有些仍然需要手工操作,而且对于关键任务还需要熟练的操作人员。基于以下三个目标:
-
通过优化制造参数,降低增材制造零件的变化性和整体表面粗糙度,使大规模精加工变得更有效、更快速
-
改进大规模表面精加工技术,以适应零件复杂性的增加
-
降低后处理成本
因此,表面处理,是决定3D打印零件能否使用的最后关卡。
为了实施上述目标,现在有各种各样的表面处理方式可供选择,并且在不断增加。但是,在多数情况下,没有单一的解决方案能实现最终的复杂零件表面处理。在对公差和表面提出更高要求的应用中,磨削可以是增材制造的有效选择,但与精密抛光技术相比,难以获得更高的表面质量。
因此,对于增材制造表面改进和抛光有多种选择,通过不同处理方式的智能组合可以带来最佳结果。对于不同行业,尤其是前沿制造领域的增材制造,根据零部件的属性不同,选用的后处理工艺也不尽相同。
①手工抛光:手工抛光质量严重依赖于操作者的经验水平,可重复性及一致性差,人力与时间成本高,并且抛光过程中产生的粉尘危害人体健康。
②喷砂:表面质量更均匀。
③离心研磨:一些机器使用离心力来增加介质施加在零件上的力,去除粗糙凸起物以实现更有效的工艺。更容易地一次处理数批零件。它们还可以配备自动介质/零件分离装置。
△ 离心圆盘精细机 图源:Belair
④振动抛光:这些机器价格相对便宜,但是形状和大小却多种多样。它们还可以配备零件进料系统和内部零件分离功能,以进一步实现后处理的自动化。
⑤拖曳抛光:实现去毛刺和抛光。也有多种尺寸可供选择,并且具有极快的时间周期。
⑥电解抛光:靠化学试剂的化学浸蚀作用对小型增材制造镂空结构或阵列结构零件表面松动易脱落的球化层的去除效果显著。化学抛光主要迅速去除表面粘附的金属球形粉末,电化学抛光在此基础上进一步降低表面粗糙度。
△ 干式电解抛光 图源:A3DM Technologies/GPA Innova
⑦ 等离子抛光:工件与抛光液中通电脱离的金属离子吸附在增材表面,工件凸起处电流冲击高而去除快,电流流动,凹凸不断变化,粗糙表面逐渐被整平。活化工件表面去除表面分子污染层,交叉链接表面化学物质。
⑧数控磨削抛光:数控磨削抛光对具有复杂内曲面、多孔结构零件的加工可达性差,一般主要用于零件外表面的清洁抛光、去除氧化层等。
⑨自适应磨削:是通过调整接触头的形状来确定磨抛加工接触面的形状,使磨抛加工实现以接触面为磨抛作业面的加工过程,提高了磨抛加工的效率。
△ 经后处理的零件表面效果
⑩ 超声清洗:通过超声清洗去除影响零件功能的污染物,是为染色/电镀操作准备表面的有效方法。这些清洁系统甚至可以配置在清洁、干燥和染色室中,从而加快后处理的最后几个步骤。
⑪激光清除:激光抛光是利用高能激光束使零件表面材料重新融化来降低表面粗糙度的一种新式抛光方法。
⑫磨粒流加工:利用磨料介质中磨粒的微切削作用去除工件表面的微观粗糙峰,以磨粒流加工技术的高加工可为克服航空增材制造复杂零件表面光整加工难题提供了一条新途径。
△ 电解质等离子抛光效果 图源:深圳市晟启科技有限公司
激光选区熔化(SLM)是3D打印技术的一种,它打破传统的刀具、夹具和模具的限制,可根据零件三维数模,利用金属粉末(粒径30μm)直接获得任意复杂形状的实体零件,解决了传统制造技术难以解决的多孔、镂空、点阵等轻量化复杂结构零件的加工制造问题,特别适用于制造具有复杂内腔结构的难加工钛合金、高温合金等零件。
△ 3D金属打印汽车零部件 图源:广州雷佳增材科技有限公司
同时,该技术具有精度高、表面质量优异等特点,成型特定的材料能够达到近乎100%的致密度。制造的零件只需进行简单的喷砂或抛光即可直接使用。可使成形的零件具有很高的尺寸精度(可达0.1mm)以及优异的表面质量(粗糙度Ra可达30~50μm)。由于材料及切削加工的节省,其制造成本可降低20%~40%,生产周期也将缩短80%。
△ A为CNC 支架义齿;B 为SLM支架义齿,两组排牙方式相同 图源:南方医科大学附属口腔医院
激光选区熔化成形技术为解决我国航空、航天、船舶、汽车、能源、化工、医疗等广大制造业领域的复杂结构件减重设计及制造问题提供了一种新的解决途径。
尽管激光选区熔化成形技术几乎能够完成任意形状零件的精密制造,但其后处理的细微精度仍是精细化加工的一道难题。因为其加工的零部件表面(包括内部通道)包含AM工艺残留的粉末,初始粗糙度比较高。选择合适的表面处理系统对于组件的使用寿命和系统的整体效率至关重要。
平滑AM组件内外表面的一种方法是批量抛光。在精加工过程中,将工件浸入装有特殊加工介质的圆形工作碗中。另外,在该过程中添加了专用化合物。工作碗的振动使介质和工件以螺旋运动的方式在工作碗周围移动。介质对工件的持续“摩擦”会产生磨削/平滑效果,从而产生所需的表面质量。
△ 批量加工可有效地平滑随形冷却流道表面积
Politecnico Milano的机械和化学工程部门与Rösler Italiana S.r.l.一起评估了用于平滑AM组件的内外表面的各种处理方法(包括批量涂饰),这个过程涉及到了对不同形状和不同直径的随形冷却流道(3、5、7.5和10毫米)的零件进行质量修整、喷丸和化学支撑质量修整。三个表面处理方法的结果惊人的相似:工件表面最光滑,如相对较低的表面粗糙度读数所示,并显示出典型的化学加速精加工优势。化学支撑质量精加工方法的Ra值为0.7 µm,表面粗糙度值最低,循环时间最短。结果还表明,在垂直和水平流道中,最终粗糙度值大致相同。
△ 各向同性刻蚀轮廓包络抛光原理图
△ 钛的刻蚀轮廓包络抛光过程的轮廓与形貌演变
以钛(TA2)的超精密抛光为例,研究人员通过对电解液和击穿电压等参数的优化,实现了材料表面的各向同性刻蚀。抛光后表面粗糙度Ra值从64.1nm迅速降低到1.23nm,高效率获得了纳米级表面。
△ 各种金属材料的抛光效果图
使用人工完成原型甚至几十个零件时可能还具有成本效益,但如果生产数百甚至上千个零件时,3D打印对后处理自动化的需求就变得极为迫切。
增材制造的金属部件通常具有非常粗糙的表面,从而要采用后续加工来消除,以满足金属打印部件的最终需求。由于采用传统的后续加工工艺存在耗时、需要高技能工人和自动化程度受到限制,造成传统的后续加工工艺对自由成型部件的应用受到极大的限制。
激光抛光是一种产能高、无接触和可以完全实现自动化的一种工艺,且可以使3D打印的金属部件表面获得令人满意的效果,尤其对于形状复杂且薄壁的增材制造的金属零件。
△ 激光3D打印的AISI H11样品进行激光抛光的实物图 图源:清华大学
在激光抛光时,当物体表面被激光所辐照时,表面凸起的锋顶会被熔化成薄层,然后在表面张力和重力的作用下重新分布在谷底中。激光抛光在抛光材料的能力上由于材料性能的变化而变化,如从高反材料铝合金到高强度材料Inconel和钛合金。
自动化的解决方案可以通过一致的后打印功能提高生产效率,不过目前也只有少数的集中特定的方案帮助实现自动化后处理,如DyeMansion公司的自动清洁系统、AMT公司的表面平滑解决方案以及PostProcess Technologies的支撑去除和表面处理系统。然而,不可否认,这些系统主要是为聚合物3D打印的零件而设计。
△ Dyemansion 的设备涵盖清粉、抛光、上色等后处理环节
在金属3D打印方面,仍然采用传统制造的后处理技术。为了使这些技术进一步自动化,一些公司也开始实施机器人解决方案,可以帮助更换材料并进行零件处理。去年EOS和Digital Metal都推出了全自动生产的概念,其采用机器人进行大多数的操作过程,如安装打印基板、清粉取件以及后处理等等,目标是取代是所有手工工作,以促进连续和规模化的生产。
尽管这种发展令人鼓舞,但该领域的创新步伐还是比较缓慢。未来,先进的后处理解决方案的数量肯定会增加,从而适应不断增长的增材制造产业的发展。
△ POWERSHOT C清粉设备 图源:Dyemansion
增材制造是一项蓬勃发展的技术,尤其表现在骨科、脊柱、设备和定制市场所需的植入式医疗器械方面。
助听器发展至今日,通常需要隐藏在耳内或耳后且不引人注目。优质的定制耳廓可确保助听器牢固且隐秘地固定在耳道中,并且不会引起佩戴者的不舒适。耳廓是通过增材制造工艺或机加工为每个患者单独制造的。制造过程中造成的粗糙表面会影响佩戴的舒适性,因此必须对耳廓的表面进行平滑处理。△ CF加工3D打印耳廓案例应用 图源:佐技机电设备(上海)有限公司
等离子柔和而有效的表面处理技术不仅可以防止在后处理过程中损坏耳廓,并且能够精确地保证其形状不受影响。通常,由于耳廓内部精密的几何结构,除了人工进行表面处理以外,自动化的处理方式难以完全达到表面加工要求。通过离心式抛光机也可达到手动加工的效果,并且效率更高。
△ 图源:Lincotek
2020年5月5日,中国首飞成功的长征五号B运载火箭上,搭载着“3D打印机”。这是中国首次太空3D打印实验,也是国际上第一次在太空中开展连续纤维增强复合材料的3D打印实验。
△ 图源:空中客车公司
为了进一步了解增材制造的精加工,尤其是应用于航空航天业中的钛基和镍基高温合金部件时,增材制造在航空航天领域应用的主要驱动力在于减轻重量,运营商愿意为提高燃油经济所带来的运营成本降低付出代价。人们对增材制造的零件密度、孔隙率和晶粒结构的最初质疑正在得到克服,该技术也已经被越来越多的用于生产认证部件。
△ 3D打印航天发动机模型 图源:河北敬业增材制造科技有限公司
磨粒流研磨方法对于航天航空3D打印金属件也有良好的研磨效果,不失为一种有效的解决办法。以钛合金3D打印叶片打磨为例,作为航空飞机上的叶片,这款钛合金3D打印叶片硬度高、粗糙度差,如果不适用磨粒流抛光,会有很多死角抛不到,而且抛光效果也不均匀。
△ 图源:布莱特磨粒流
如上图为抛光前的叶片,相对来说还算细腻,表面已经做过喷砂处理。叶片的阴阳两面都需要抛光,阴面的粗糙度更差一些。针对这种叶片抛光需制作专用工装,不仅是为了保护叶片或是装夹,也是为了导流,引导流体磨料可以充分贴合叶片曲面以及进入每一个型腔。
不同于一般的产品抛光,钛合金3D打印件的抛光时间要长很多,通常这样一个产品磨粒流抛光的时间为30分钟到1个小时,视产品大小及粗糙度情况而定。
△ 图源:布莱特磨粒流
抛光完成后,钛合金叶片表面已经有了镜面光泽。完全将表面的凹坑去除是不现实的,凹坑的深度肉眼可见,完全去除的话叶片的精度就没有了。但是目前这个状态,已经不会掉渣或是在快速转动过程中形成阻力了,因为表面已经呈现流线式光滑面了。
△ 3D打印铝热交换器 图源:PWR
汽车工业是国家经济发展的支柱产业,汽车零件同样也是形状复杂,加工制造难度大,汽车领域作为金属打印的主要应用领域之一,正在受到越来越多的重视。差异化层厚、模具尺寸精度和表面质量的高要求,是3D打印汽车零部件表面打磨抛光的重要基准。
△ 3D打印轮胎钢板模具 图源:EPLUS3D
无论是铝制热交换器,还是铝制进气歧管,3D打印零件经过分层处理后, 具有明显的表面结构,其特征是表面具有条纹、细孔、裂缝和空洞。改善表面质量和减少阶梯效应,是解决增材制造汽车零件表面问题的切入点。而适用于这些打印金属零件的表面处理方法是多样性的,其工艺取决于零件孔道的复杂程度。
如燃油喷嘴的增材制造在缩短制造周期、降低制造成本以及提升合格率方面具有明显优势,但是喷嘴内流道表面的光整处理成为打印工艺亟需突破的关键技术难题。磨粒流抛光可有效去除表面黏粉、球化现象,改善表面台阶效应,明显降低喷嘴内流道表面粗糙度。
△ 3D打印复杂的铝制进气歧管 图源:福特公司
△ 德国国航天中心 Smile 项目点火测试
现代化军事特点不仅仅是机械化、信息化,还要有快速的创伤修复能力,比如战场机械的修复以及辅助工具的帮助,而这些零件和工具在机动性强、变化迅速的战场会变成负担,并且损伤零件的不确定性和辅助工具的不通用性,都会制约战场的作战效率。而增材制造技术可以有效地解决这些问题。
△ 3D金属打印推进系统 图源:3D SYSTEMS
比如,在推进系统方面,3D打印能够减轻火箭引擎和太空卫星引擎的重量。不同于传统制造,直接金属 3D 打印技术能够最大程度利用空间和材料的喷嘴、燃料预燃器、阀门、歧管以及其他推进系统。如此一来,便可实现功能改进,同时减少生产时间,降低成本,并减轻部件重量。
△ 3D金属打印热换器 图源:3D SYSTEMS
△ 3D金属打印射频 (RF) 无源硬件 图源:3D SYSTEMS
再比如在热交换器方面,3D打印可优化传热组件制造,从而缩短交货时间,降低成本并提升性能。并针对需要多个薄壁面、较大的表面体积比和极为严苛公差的关键热管理部件实现性能增强。
对于以上喷嘴、燃料预燃器、阀门、歧管、热交换器,您觉得使用哪一种抛光或者打磨技术,能够更好地实现优化内孔管道和外表面质量,进而提升组件可靠性呢?
主编微信:2396747576(请注明身份); 硕博千人交流Q群:248112776;网址:www.amreference.com
延伸阅读:
4.2023 TCT亚洲3D打印展预约全面启动,看透技术、材料、应用与市场现状