空客巨资开发起落架结构部件3D打印,以替代大型锻件
9月1日,3D打印技术参考注意到,空客联合其他15个合作伙伴(从行业领导者到小型企业、学术界和研究组织)发起了一项名为I-Break(起落架工业突破)的项目,旨在采用粉末热等静压、增材制造和复合材料等创新技术,特别是来自WAAM3D的电弧增材制造技术,开发和制造目前使用大型锻件生产的主要起落架结构部件。
该项目将耗资2250万英镑,I-Break项目将开发适用于准备投入使用的下一代飞机制造解决方案。所有这些技术都是为了缩短飞机上市时间并将工业二氧化碳排放量减少30%。
采用3D打印技术制造起落架的尝试并非首次,国内外均进行了长时间的研究,并取得了重要进展。
新华网于2013年就已报道过,中航工业副总工程师、歼-15总设计师孙聪在接受新华社专访时透露,钛合金和M100钢的3D打印技术已广泛用于新机设计试制过程,其中包括整个前起落架。
无论起飞还是降落,起落架都是支撑飞机的唯一部件,尤其是在飞机降落阶段,其承载的载荷不仅来自机身重量,还有飞机垂直方向的巨大冲力。因此,起落架的材料强度必须十分优异。此外,由于复杂的受力情况,起落架材料还必须具有超韧性、抗疲劳和和耐腐蚀的性能。
现代大型客机多采用支柱套筒式起落架,由外筒和活塞杆套接起来的缓冲支柱组成,机轮直接连接在支柱下端,支柱上端固定在飞机机体骨架上
传统上,起落架的主要承力构件均采用大型整体锻件进行制造。材料多选用低合金钢、钛或铝的合金,如波音787起落架主支柱外筒采用300M钢锻件,缓冲支柱活塞杆是钛合金整体锻件,这种整体的结构取代拼焊结构,能够有效提高寿命。在材料性能方面,300M钢的抗拉强度很高,达到1860Mpa,其横向塑性、断裂韧性和抗疲劳性也都很高,是大型飞机起落架的主导应用材料。钛合金因重量轻、强度高也被广泛用于起落架主承力构件上。
起飞过程起落架工作情况
起落架钢材料多采用真空感应加真空自耗重熔,材料冶炼成本高,因此材料价格较高。而起落架外筒及活塞杆为筒状构件,采用传统锻造+机加的制造方法,筒内实心部分需要采用深镗切削加工去除,易造成材料浪费,且加工难度大,制造周期长;特别是面对当前飞机型号的快速试制时,采用锻造工艺制造起落架将面临原材料尺寸规格限制、不利于快速响应等诸多技术问题。另外,当前的加工方法也限制了部件结构设计,从而使强度重量比无法得到有效改善。因此在满足材料性能的前提下,如何节约成本和简化工艺成了一个亟需解决的问题。
2021年,在赛峰集团与SLM Solutions的一个联合项目中,双方采用选区激光熔化技术制作了一款商务喷气式飞机的前起落架组件,采用SLM技术来3D打印制作如此大尺寸的飞机部件,尚属世界首次。该项目的目标是证明通过SLM 3D打印技术生产主要配件的可行性。与传统起落架零件通过5轴加工和三个锻造零件组装而成相比,为适应3D打印逐层制造的工艺特点,需要将组件进行重新设计,这不仅节省了整个制造过程的时间,最终还将原来的三个零件组合为一个整体,重量减少了约15%。
作为将载荷从车轮传递到飞机结构并在起飞后缩回的部件之一,赛峰对该零件的性能有严格的要求,因此材料选择了钛合金,它不仅强度高、耐腐蚀,打印后的表面质量也能够达到使用要求,仅需对功能表面进行机械加工。相比能量沉积技术,后者虽也能制造大尺寸零件,但仍需大量的后期加工才能满足使用要求。
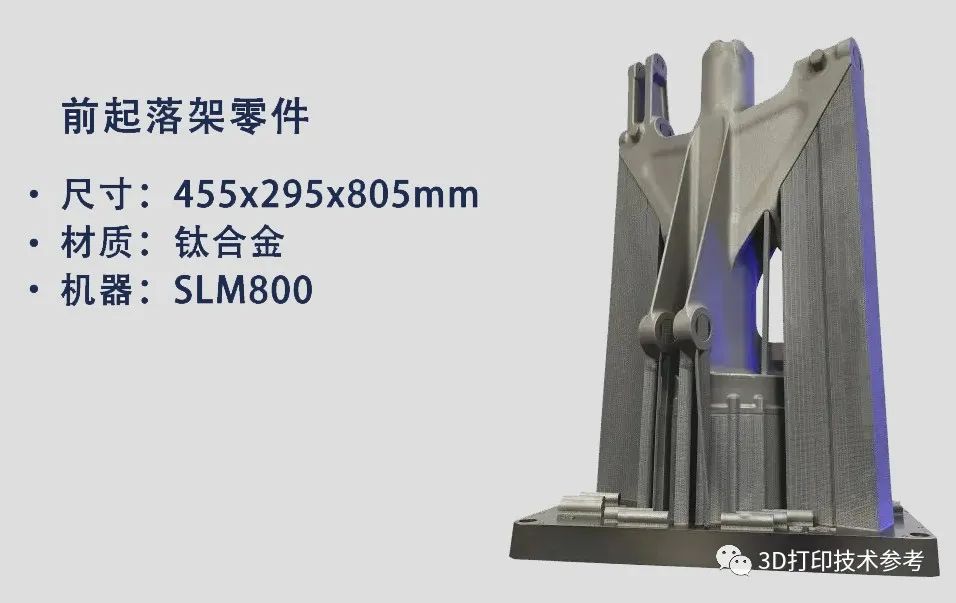
I-Break项目通过英国航空航天技术研究所 (ATI) 计划提供支持,并由英国政府一项更大的计划提供资金,其中2.18亿英镑已分配给突破性的航空航天研发项目,支持全国各地的就业和增长。
航空航天技术研究所首席执行官Gary Elliott最近表示:“工业部长Nusrat Ghani在巴黎航展上宣布通过ATI计划进行的投资将支持一系列世界一流的技术研究项目,以提高航空航天的可持续性,从新的设计工艺到新材料。”
与SLM技术相比,电弧增材制造具有更高的制造效率,近些年来正在呈现应用加速阶段。WAAM3D在I-Break中的作用是围绕更高生产率的电弧增材制造工业化生产;控制高完整性结构应用的微观结构和机械性能;在线无损检测技术产业化;并在其升级后的RoboWAAM系统上生产相关尺寸和复杂演示部件。
I-Break项目包括多个工作任务,其他合作伙伴包括克兰菲尔德大学致力于新型 WAAM工艺和解决方案,以及关键新合金的验证;斯特拉斯克莱德大学致力于创新在线无损检测技术;世界领先的高性能传统和相控阵超声波仪器设计商和制造商PeakNDT致力于在线无损检测硬件系统。I-Break项目目前预计于2026年完成。
主编微信:2396747576(请注明身份); 硕博千人交流Q群:248112776;网址:www.amreference.com
延伸阅读:
1.赛峰与SLM Solutions合作3D打印大尺寸商用飞机前起落架组件
2.聚焦中国航空航天增材制造 ▏众多大咖分享一线3D打印技术应用现状
3.首都航天机械有限公司实现超大尺寸铜合金产品的高效增材制造
4.逐梦苍穹,回顾GE航天航空增材制造之旅,中国航天航空能否弯道超车?