研究:通过改善铺粉质量提高高反射金属3D打印过程中的能量利用率
2023年2月17日
2K
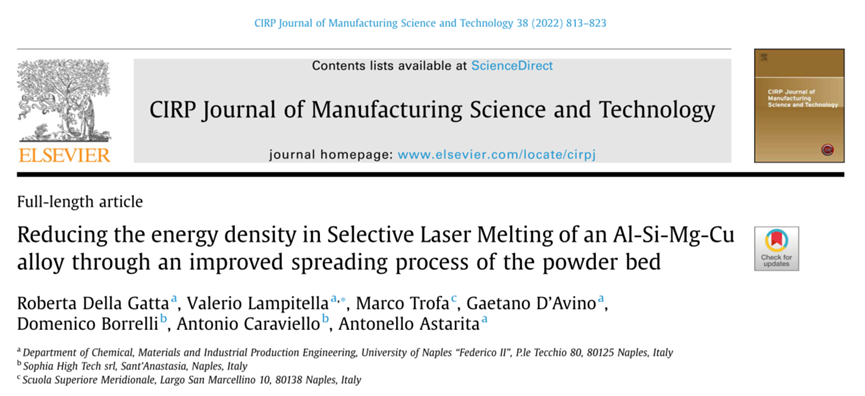
原文链接:https://doi.org/10.1016/j.cirpj.2022.06.017
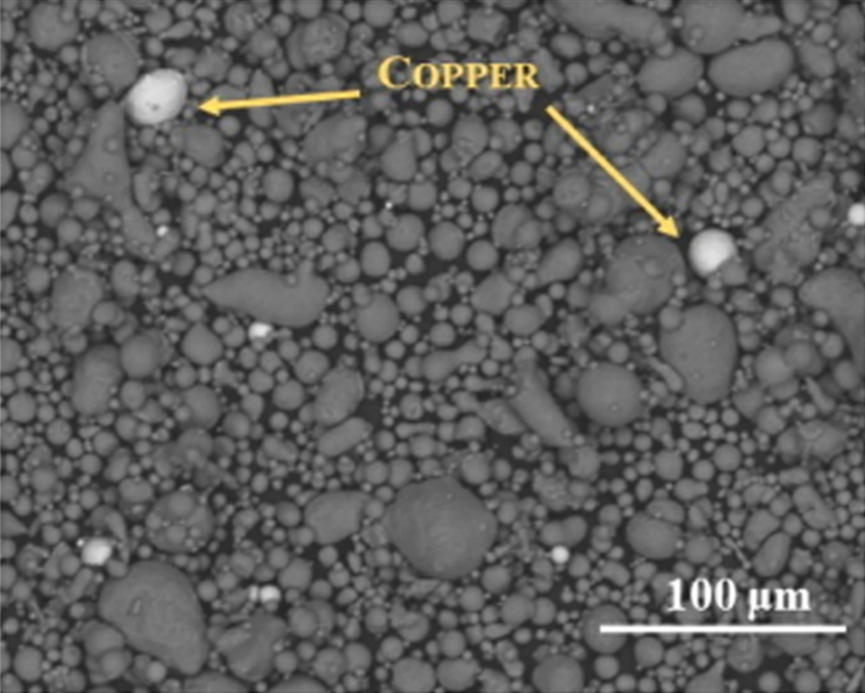
30μm层厚下不同铺粉速度模拟结果:(a) 75mm/s;(b) 50mm/s;(c) 25mm/s
SLM制备样品工艺参数
不同激光功率下样品相对密度和孔隙率
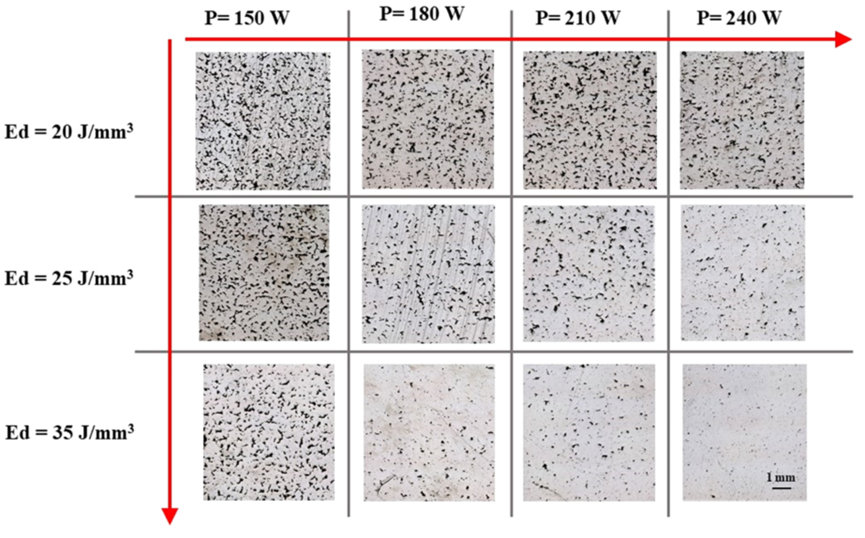
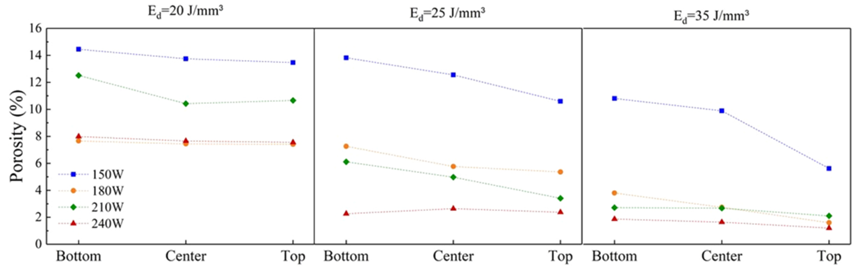
SLM制备样品不同部位孔隙率变化
主要研究结果为:Al-Si-Cu-Mg原料合金通过流化床将AlSi10Mg和Cu粉末均匀有效的混合。建立的离散元方法模型用于研究粉末铺展过程特性,并对铺展速度和层厚的最佳值进行探究。通过改变激光参数来研究打印过程,以探索在低能量密度下Al-Si-Cu-Mg的可打印性。尽管在最低激光功率下存在不同缺陷,但打印样品显示出良好的致密度。样品从底部到顶部的孔隙率略微降低,表明当层数增加时,实际层厚度增加,对样品的可打印性具有积极的影响,这是打印零件机械性能变化的一个可能原因,因为底层粉床条件变化,而激光参数不变。最后,AlSi10Mg和Cu粉末完全熔化并混合,相关参数定义了获得完全致密零件的最低要求。
总的来说,这项研究提出一种粉末铺展模拟和激光打印样品的综合方法,以降低高反射材料SLM中的能量消耗。研究了工艺参数对Al-Si-Cu-Mg合金可打印性的影响。强调了SLM工艺中粉末铺展的重要性,将打印样品的特性与粉末层的铺粉状态相关联。然而,这项研究只模拟了粉末数量相对较少一部分铺粉过程。此外铺粉过程仅限于具有平坦基底的第一层,需要进一步研究来改进数值模型,并提供对粉床特性更加真实的预测。
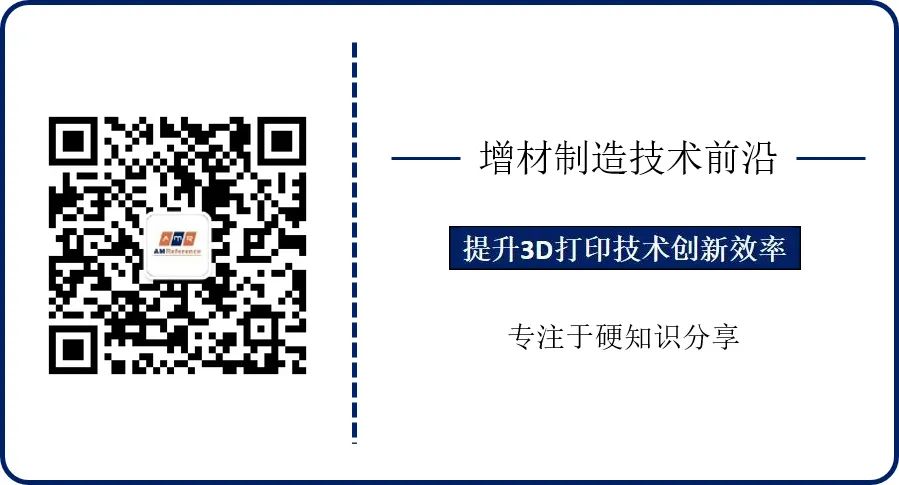