
导读:只有在稳定的制造条件下,金属注射成型或采用粘结剂喷射3D打印工艺(如粘结剂喷射)生产的烧结零件才能达到一致的高质量。然而,烧结炉中的不均匀和瞬态温度是难以控制的重要变化因素。
在开发和生产部件时,必须找到相对最佳的设计或制造条件,特别是在价格压力和质量要求的背景下。由于时间、资金的限制,在这些领域达到绝对的最佳状态是不可能的,只能缓慢持续改进过程。对于粘结剂喷射3D打印技术成形的零件,通常首先需要将零件进行脱脂,在该过程中大部分的粘结剂会被去除。
然而,烧结炉内的瞬态和不均匀状态会对烧结件产生影响。特别是,烧结零件内的温度梯度是各种问题产生的原因。因此,随着烧结零件尺寸的增加,这些问题变得更加复杂。同时,不均匀的热输入还会造成粘结剂降解不均匀的后果。烧结炉的高质量烧结只能通过在受控条件下稳定的制造工艺来实现,从成型开始,到烧结结束。
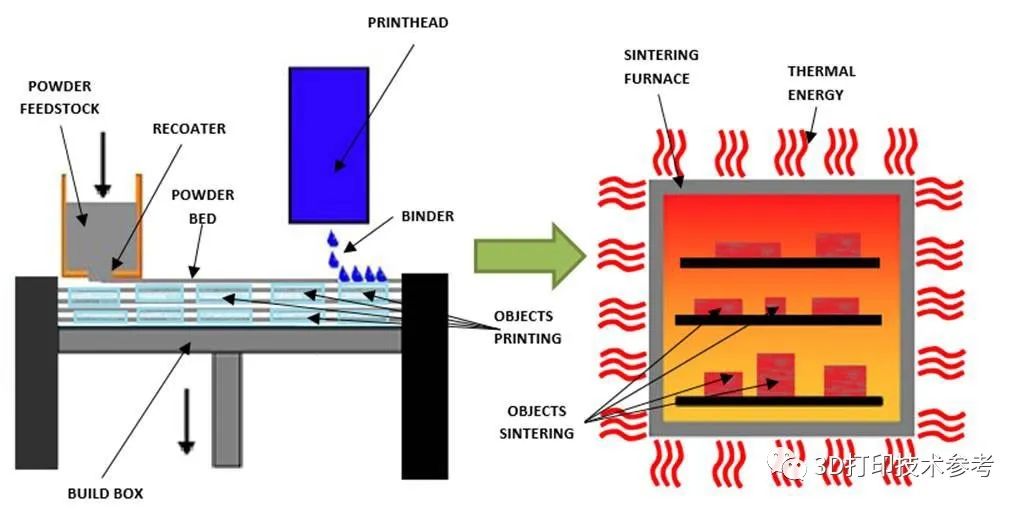
对于粘结剂喷射3D打印来说,在工业烧结过程中,单个烧结部件的温度随着时间的推移而变化,并根据它们在炉中的位置而变化。这意味着在烧结过程中,每个烧结部件都暴露在单独的瞬态温度环境中。
在烧结阶段开始时,部件由于放置的位置不同,温度相差可超过30℃。同时,中间的零件比靠近炉膛加热的零件晚20分钟以上达到所需的烧结温度。这证明,即使在烧结过程中保持炉温,也会导致每个烧结部分的瞬态、不均匀的温度环境。
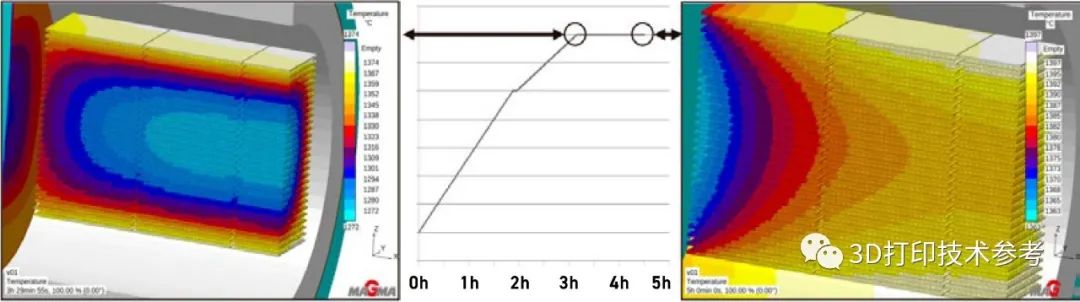
炉温刚刚达到1400℃时(左)和保温时间结束时(右)的烧结件温度
仿真计算的结果显示,在3.5小时后,炉内各处应达到1400°C的目标温度,然后在炉内保温1.5小时。然而,计算显示出不同的结果:烧结部件之间的温度分布明显是不均匀的,当炉温刚刚达到1400°C,温度差异100°C,结束的时候保持时间共计5小时后,温度差异仍高达34°C。在这个例子中,辐射热源在1400°C,在真空烧结的情况下,决定变量是炉内所有区域、置物架和烧结部件之间的热辐射,以及模型中所表示的所有部件内部的热传导。计算表明,在加热开始时,面向受热体的烧结部件暴露在高达3500w /m2的高热流中,而放置在炉中央的烧结部件几乎没有接收到热量。热量从炉管散发出来,被炉壁、炉门内侧、炉架和烧结件吸收。发射或吸收的问题产生于辐射能交换的表面的温差。
在加热阶段结束时,炉内某一段的烧结部件的温度。左边边界是炉中心,右边边界是炉侧的加热管
仿真定义了两个特征阶段:第一阶段是加热阶段,在该阶段,样品的导热系数由钢颗粒的热传导和它们之间的辐射的温度依赖效应决定;第二阶段是等温烧结阶段,导热系数由同样的效应决定。考虑到粉末颗粒在烧结过程中形成越来越致密的结构时,热传导量的增加。在烧结过程中,从烧结开始到烧结完成,导热系数随密度的增加而增加,从40%到100%呈线性变化。在保温阶段,仍有相当大的热量交换,这是由于炉内永久存在的温度梯度。
烧结炉内的温度分布在任何时候都是不均匀的。考虑到这一点,应该提出有关工艺改进的问题,以便在烧结过程中更接近稳态和均匀温度。然而,开发、测试和实现可使炉温更均匀的替代加热概念当然是有风险的、耗时的和成本高的。
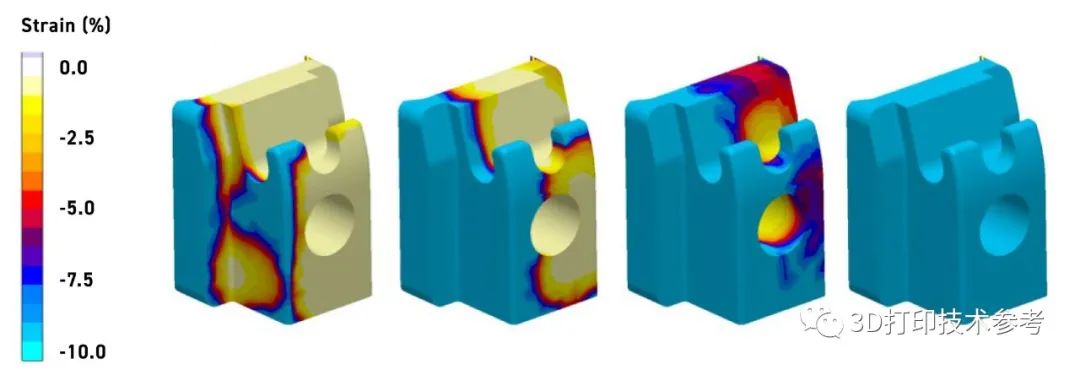
粘结剂降解过程中生坯的瞬态局部应变
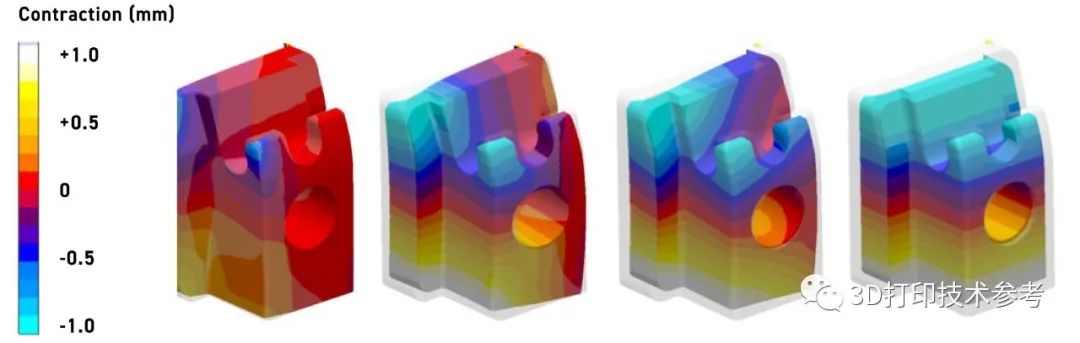
在重力作用下蠕变和基底上自由滑动会产生瞬态局部收缩
对于注射成型和粘结剂喷射3D打印零件的热脱脂过程中,粘结剂不均匀分解和由此产生的不均匀瞬态应变和应力,可能会使零件中出现缺陷。例如,不均匀、单侧暴露在高温下下的生坯部分会面临特殊风险,会导致生坯部分的特征性伸长;在重力作用下蠕变和基底上自由滑动会产生瞬态局部收缩。
实际上,烧结变形,已经成为一些从事粘结剂喷射3D打印技术开发的企业面临的主要难题。金属粘结剂喷射技术对材料、粘结剂以及打印工艺(包括粘结剂的喷射量、粉末中的压力分布、沉积时间等)、烧结制度、零件设计等等有着重要的依赖关系,技术含量并不比SLM低。与此同时,该技术所制备的零部件存在两个主要缺点:一个是在烧结过程中零件的非各向同性收缩问题;另一个是由于零件重量与烧结制度匹配不佳所带来的潜在变形问题,这会限制所能成型的最大零件尺寸。此外,还有一个不可忽视的因素是设备成本问题,后工艺阶段的脱脂烧结炉,比3D打印机贵的多。