西门子端到端增材制造解决方案
有内容 有深度 有态度 欢迎关注
当前,增材制造已成为材料制备科学和先进制造技术学科领域国际前沿研究和竞争热点之一,也是企业实现数字化制造期待实现的首选制造技术。它改变了产品的制造方式,得到了多领域制造业巨头的青睐。本期,我们来看西门子如何使用这一技术,并介绍其端到端的增材制造解决方案。
制造行业对工业新技术的需求
▌西门子端到端的增材制造解决方案
目前市面上的增材制造功能软件功能单一,只注重3D打印的制造输出部分,缺乏面向增材制造特点的设计、仿真和流程管理,众多客户只能选择很多不同厂家的软件拼凑在一起,这种多个软件的来回繁琐操作会带来数据转换丢失,流程和数据管理困难,无法实现仿真拓扑优化快速实时修改设计的闭环,生产效率无法提高,大大制约了增材制造的大规模工业化应用。
增材制造产业化的现状
一个完整的增材制造平台已经成为工业领域普及增材制造技术的关键。西门子公司把软件和机床系统解决方案同增材制造进行集成,已经为增材制造开发了一个端到端的设计建造开发平台,涵盖从概念、设计、制造到车间操作及自动化的所有过程。在西门子提供的增材制造系统平台中具备传统三维CADCAECAM能力,同时推出了拓扑优化设计、针对多种3D打印方式的工艺辅助设计准备、输出、校验,增材制造设备连接处理器等崭新专业功能。
西门子完整的一体化增材制造系统平台,通过重塑设计、重组制造、重构业务,着力于实现增材制造的工业应用。
西门子增材制造端到端解决方案
▌面向增材制造的创成式设计
西门子采用创成式设计技术,可以从产品设计开始就将性能需求纳入考虑,生成可以满足所有性能需求的最优轻量有机形状,在设计零件的几何图形和拓扑时提供不受限制的自由度。新的创成式设计技术可以减少重量和材料,甚至具有性能优势。
对传统设计零件进行重塑的工作流
拓扑优化技术-西门子的拓扑优化包括面向设计师直接集成于NX CAD的Topology Optimization for Designers和面向分析师的Simcenter Nastran Topology Optimization,两者都提供在特定的设计空间生成满足各种产品性能、材料和制造需求的创新性结构,通常所产生的结构形状更适合于增材制造技术。
西门子面向设计师和分析师的拓扑优化技术
收敛建模™技术:对于工程师而言,这一创新技术大大简化了由小面体、曲面和实体组成的几何图形的处理过程。这个创成式设计方法可以帮助工程师优化用于 3D 打印的零件的设计,并且加快整个过程。
从扫描到打印-通过使用收敛建模技术,用户可以立即开始用扫描的数据来设计产品。通过将收敛建模与直接由 NX 提供的 3D 打印制造零件的能力结合起来,简化了增材制造过程。这个新的“扫描 -编辑 - 打印”工作流支持 3D 制造格式(3MF)和微软的 3D 打印功能。
收敛建模实现了“扫描到打印”工作流
晶格设计:集成的晶格结构设计,使用晶格命令可创建轻量级结构收敛体,这些收敛体可以使用增材制造技术生产。您可以选择多个不同单元格类型,并指定单元边长度和杆径。还可以指定晶格的放置和方位等。
NX晶格设计
3D打印设计规则:验证用于 3D 打印的设计是整个过程中的一个关键步骤。NX 提供了用于检查下列内容的验证工具:
•可以规定最小壁厚,确保零件的可打印性
•可以用悬垂角度来识别在打印时需要支撑的零件区域
•可以识别全封闭体积,确保对这些区域可进行高效的打印后处理
•可打印体积能够快速计算零件是否与打印机打印体积匹配
这些验证工具可以帮助进行数据准备,确保设计零件的可打印性。
拓扑优化考虑基于增材制造工艺的产品设计规则,以确保产品的可制造性。
基于增材制造工艺的产品设计规则
▌面向增材制造的性能及工艺仿真
仿真工程师能够用 Simcenter™ 产品组合进行增材制造产品的性能仿真,以确保产生的结果满足所有必要的性能标准。工程团队可以用 Simcenter™ 产品组合满足结构强度、热、流体动力学、振动噪声、电磁、多体动力学、疲劳等各种性能要求。
基于增材制造设计的产品性能验证和优化迭代
Atlas 3D面向设计师的增材制造工艺仿真:
3D 打印的高失败率是企业利用增材制造实现批量生产需要面对的关键挑战之一。零件通常需要经历多次设计和分析迭代,才能确定最优构型取向和优化的支撑结构。通常,结构设计师无法胜任同时考虑零件设计的优化、结构变形和散热均匀性的多学科综合分析,于是解决这些问题的重担便落到了工程专家的肩上。
西门子近期完成了对Atlas 3D, Inc. 公司收购协议的签署。Atlas 3D 公司的 Sunata™软件通过为前端设计师提供一种简单快捷的自动化方法,使其能够更接近“首次即正确”的创成式设计,从而解决这一问题。
• Atlas 3D 可帮助设计师确定最优零件制作方向,实现3D 打印“首次即正确”。
• 基于云的 GPU 加速 Sunata 软件,可减少因热变形而造成的下游3D 打印错误,速度比市面上其他解决方案快百倍。
Atlas 3DSunata面向设计师的快速增材制造热变形分析
Sunata™ 软件利用热变形分析技术,为用户提供简单的自动化方式,助其优化零件制造方向并建立支撑结构。通过此方法,设计师(而非分析师)可以执行仿真模拟,最终交付满足设计要求的零件。西门子计划通过其增材制造网络在线平台(Additive Manufacturing Network)提供 Atlas 3D 解决方案。
Sunata 是一款 GPU 加速的高性能计算增材制造软件解决方案,其结算分析速度比市面上的其它创成式仿真解决方案快达百倍。GPU 加速计算是指同时采用图形处理单元(GPU)和计算机处理单元(CPU),以推动深度学习、分析和工程应用等过程密集型操作。
借助于Atlas 3D 解决方案,设计师可以快速洞察相关的最优零件制造方向,进而将支撑结构、变形、移除支撑结构的难度、零件物料以及打印时间减少至最低水平。
Simcenter 3D AM面向分析师的增材制造工艺仿真:
Simcenter 3D AM增材制造工艺仿真解决方案,用于预测增材制造工艺过程中的各种问题,并完全集成与西门子NX端到端的增材制造解决方案中,可以帮助制造商大规模设计和打印有用的零件。该解决方案使用数字双胞胎模拟打印前的构建过程,预测打印过程中的变形并自动生成校正后的几何以补偿这些变形,对于构建“首次正确”打印至关重要,并且是实现工业化的增材制造工艺所需的效率所必需的。
Simcenter 3D AM集成于西门子端到端的增材制造解决方案很大的优势在于可以实现仿真与设计及制造的无缝连接和快速优化迭代循环。工艺仿真的输入和输出是从初始需求到最终零件打印这一连续数字主线中的一部分,这一连续数字主线可以允许系统提前生成变形补偿的模型,并无缝传给产品设计及打印制造。
Simcenter 3D AM面向分析师的增材制造热变形分析
Simcenter 3D AM提供增材制造工艺仿真的高度自动化流程,通过创建包含打印零件、支撑结构和粉末的打印工作台数字化双胞胎模型,模拟整个打印工艺过程,提前预测可能出现的零件变形并自动进行变形补偿,并预测局部过热、收缩线和刮板碰撞等打印问题,为制造商调整打印工艺参数,提升打印质量提供了很好的保证。
Simcenter 3D AM完全无缝集成于NX AM,并采用数字双胞胎模拟打印过程,可以预测温度场、局部过热、打印变形、自动变形补偿、刮板碰撞、刚度计算等。将 Sunata 软件与Simcenter 3D AM强强联合,能够实现工业3D 打印的‘首次即正确’。
Simcenter Star CCM+面向增材制造的工艺和性能仿真:
增材制造过程的特点是其多物理场特性,Simcenter STAR-CCM+能够很好的模拟增材制造过程中流体和固体的传热问题,包括模拟湍流现象及其对共轭传热问题的影响。Simcenter-STAR-CCM+一流的运动模型,其特有的Overset Mesh重叠网格功能或Mesh Morpher网格变形器,可以用来模拟3D打印机送粉运动及与周围环境的相互作用。通过Simcenter-STAR-CCM+的多相流和相变模型,可以模拟在激光束的作用下,粉末进入熔池并逐步固化的过程。
Simcenter STAR-CCM+可以模拟增材制造的工艺过程,如粉末床熔融、定向能量沉积、材料挤压(Material Extrusion),并能够用于增材制造设计领域,如设计评估、3D打印机热可靠性、换热装置及随形冷却水道设计等。
Simcenter Star CCM+在增材制造领域的应用
Simcenter & Heeds结合面向增材制造的优化设计:
Simcenter还可以和Heeds结合,利用Heeds强大的SHERPA优化算法进行设计空间探索。比如通过DOE或单目标及多目标优化来实现随形冷却水道的优化设计。
Simcenter Star CCM+和Heeds结合进行随形冷却水道设计优化
▌增材制造设备连接
西门子为塑料、金属产品的多种增材制造方式的规模生产提供技术保证,能够连接粉层熔融、固定多轴材料拉丝、HP多喷射设备,同时能够将3D打印与传统制造技术融为一体,使用铣、钻、镗、磨等传统减材工艺与3D打印增材工艺于一体的“混合型机床”进行制造。
西门子支撑多种增材制造技术
西门子推出的打印建造托盘、嵌套零件,支撑结构等功能能够快速高质量完成批量化3D打印制造,大批量的工业产品3D打印量产将能够大大简化传统制造工艺,减少工装装备环节,节约大量毛坯材料,最小化产品制造周期时间。
▌增材制造生产运营管理
西门子为增材制造生产过程提供全程的过程管控,能够管理所有3D打印的准备和后期生产,进行全生产过程数据跟踪,管理所有加工数据和过程、数据的重用。包括订单管理、操作指导和审核流程、打印作业文件管理、打印材料管理等,提供一个闭环的全生命周期管理。
▌增材制造的工业实践者和领导者
西门子完整的一体化增材制造系统平台同时致力于将软件和实际工厂经验相结合,已投资约2亿瑞典克朗,在瑞典Finspn开设一间大规模制造金属3D打印部件的工厂。这不仅是瑞典国内的首家此类工厂,也标志着西门子首度正式进军金属3D打印部件的工业生产领域。同时西门子已经获得MaterialsSolutions公司85%的股权。Materials Solutions是将选择性激光熔融 (SLM) 技术用于高性能金属部件制造的先驱,在英国Worcester经营着世界上最大的商用金属增材制造中心,客户群遍及全球。在涡轮机部件的增材制造有丰富经验。因此西门子有能力将实际规模生产的经验融合到商业化的增材制造系统平台中。
西门子公司用于实际生产的增材制造
2017年,西门子成功完成对完全采用增材制造(AM)技术生产的燃气轮机叶片的首次满负荷核心机试验,实现技术上的重大突破。西门子在发动机满负荷状态下成功验证了多个采用传统设计的增材制造涡轮机叶片。这意味着该叶片的测试转速达到每分钟13,000转,测试温度超过摄氏1,250度。此外,西门子还测试了利用增材制造技术制造的经全面改良内部冷却结构的新叶片。
这些叶片安装在13兆瓦(MW)的西门子SGT-400工业燃气轮机上。该增材制造轮机叶片利用多晶镍超合金粉末制造,能够耐受高压、高温和燃气轮机的高速运转所产生的离心力。在满负荷核心机试验中,这些燃气轮机叶片运行速度超过1,600公里/小时,受力高达11吨(相当于伦敦一辆满载公交车的重量)。这些叶片被摄氏1,250度的气体包围,然后利用超过摄氏400度的空气冷却。在林肯工厂测试的先进叶片设计改进了冷却性能,可以提高西门子燃气轮机的总体效率。这是增材制造在发电领域应用的重大突破,对增材制造技术来说也是最具挑战性的应用之一。
▌西门子端到端增材制造解决方案的优势
西门子通过重塑设计、重组制造、重构业务,在单一的集成系统中无缝集成设计、仿真和3D 打印规划,能够满足最新增材制造工业化应用的独特需求,帮助企业快速从传统设计制造升级到增材制造生产方式,大幅提高增材制造量产的准确率和生产效率。
• 西门子提供最完善的端到端软硬一体化集成软件平台,并且能够与实际商业生产经验相结合。
• 西门子基于智能的模型驱动流程,实现从设计到3D 打印量产的无缝工作流程,消除不同软件之间的数据转换。
• 西门子将下一代设计技术—创成式设计纳入数字化设计中,自动化的结构优化能更好满足产品的功能和性能需求。
• 西门子提供强大的面向增材制造的性能及工艺仿真和优化技术,帮助客户实现“首次即正确”的打印。
• 西门子支持多种3D 打印技术,能够连接多种3D打印技术和设备,西门子为增材制造的规模量产提供了可落地的可靠技术保障。
• 西门子正在构建一个非凡的世界领先合作伙伴生态系统,并与他们一道推动增材制造的革新。
• 西门子通过咨询、工程和打印服务,向客户分享其的经验,帮助客户应用增材制造。
注:本文最早见于Converge Online,本期上传:西门子增材制造解决方案高层速览
4.3D打印产业链:正在由导入期迈入成长期,行业整体毛利率较高
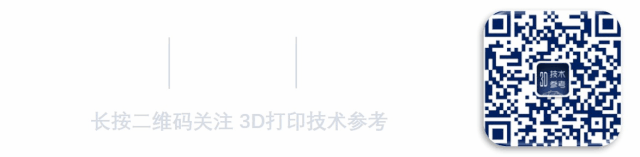