国内打印尺寸超400*400mm的SLM品牌、问题、优势及发展的内在驱动力
有内容 有深度 有态度 欢迎关注
本文所叙述的不仅仅是打印幅面超过400×400×400mm的SLM设备品牌及产品,还包括大尺寸打印不得不关注的几点问题,国内在大尺寸打印幅面方面呈现火爆现象的内在驱动力,以及大尺寸打印所具有的的优势和面临的风险。
▌国产大尺寸SLM打印机品牌
铂力特
据铂力特相关资料介绍,该公司目前已推出两款具有大成型幅面的SLM设备。其中,BLT-S500成型尺寸400×400×1500mm,首次在全球实现单向1500mm级大尺寸SLM 3D打印,主要面向航空航天长轴类零部件定制开发。目前,已实际打印出最大尺寸1200mm的世界最大单方向尺寸的钛合金制件,是目前全球范围内可见报道中打印高度最高的设备。
BLT-S500打印的航空发动机风扇叶片,钛合金,400*400*780mm,200h
BLT-S600主要面向航空航天大型回转体类零部件定制开发,实现了三向600mm大尺寸3D打印,是目前全球可见报道中最大回转直径商业化金属3D打印设备,目前已打印出直径近600mm的高温合金零件,成形尺寸、成形精度处于国际先进水平。
铂力特大尺寸金属3D打印产品
铂力特自2015年启动上述设备研发工作,设备拟自用为主。截至2019年上半年,公司生产自用转固S600 2台,在产S500 12台、S600 6台,实现S500设备销售1台,在手订单2台,S600尚未有对外销售订单。
易加三维
2016年,北京易加三维“大尺寸粉末床选区激光熔化增材制造工艺与装备研发”项目获得该年度国家重点研发计划“增材制造与激光制造专项”1985万元的经费支持。今年10月,易加三维在其金属增材制造用户大会上首次对外公布大尺寸金属打印机EP-M650,该产品系定制机型,成型尺寸为600×600×600mm,目前已成功应用于航空航天、军工和轨道交通领域。
易加三维大尺寸SLM研发机EP-M500
上海探真
2016年,来自华中科技大学武汉光电国家实验室的技术团队通过湖北省科技厅“大型金属零件高效激光选区熔化增材制造关键技术与装备”的成果鉴定。同年,上海探真成立,针对日益增长的以航空发动机叶片为代表的大尺寸工件的3D打印需求,该公司于2018年发布成型尺寸为500×500×1000mm 的大型SLM设备TZ-SLM500。实际上该设备即当年科技转化的成果,目前已迭代2次,生产多台,自用1台。
TS500打印的商发全尺寸航空发动机风扇叶片,304L不锈钢,308*341*724mm,170h
华曙高科
华曙高科目前已上市的大尺寸SLM设备为FS421M,成型尺寸425×425×420mm。FS721M是该公司已开发但未发布的最大型SLM设备,成型尺寸720x420x400mm。
其他及在研设备
此外,天津镭明开发的最大成型尺寸的SLM设备为420×420×530mm,苏州西帝摩为500×500×500mm和750×750×500mm两款。汉邦正在研发的一款最大成型尺寸的金属打印机为600×600×1000mm,苏州倍丰在研600×500×500mm成型幅面的设备。
▌大尺寸SLM打印机须关注的问题
大尺寸SLM打印机大都突破了四光束联动扫描与拼接等关键技术,采用可移动成型缸。但用户还需考虑设备是采取上送粉还是双缸送粉,双向铺粉还是单向铺粉,毕竟如此大型的设备,粉末的固定成本亦是相当高昂,采取双缸送粉将限制实际的打印高度;而采取单向送粉,则会限制大幅面打印情况下的制造效率。同时也须考察设备是否具备在线监测功能,四象限加工的质量均一性和稳定性,重合区的制造质量控制等问题。
四激光打印分区
在此前我们也曾关注光束的稳定性问题。在打印超高零件时,不稳定的光束可能会造成零件打印错位;多激光的扫描次序与分配方案会直接影响残渣在风场条件下能否被全部带离打印平面;随着打印高度的变化,多激光、振镜系统能否在设备硬件热量变化和环境温度变化状态下一直保持较好的稳定或平衡状态,等等这些问题均会影响到实际的打印质量。
▌为什么国内的大尺寸SLM打印机研发呈繁荣态势
目前,国际知名的SLM设备生产商拥有的大尺寸打印机分别有EOS M400(400 × 400 × 400 mm),SLM Solutions的SLM800(500 x 280 x 875mm)、concept laser X line 2000R(800×400×500mm)、1000R(630 × 400 × 500 mm),以及3D Systems DMP Factory 500等等。
3D Systems DMP Factory 500
国外的大型设备虽不少,但这并不是国内设备商纷纷开启研发的根本原因。在国内SLM设备领域,业内人员基于对EOS品牌的信赖而一直是其产品的跟随对象,但后者最大成型尺寸的打印机也不过如此。造成今天如此情形的根本原因还是在于来自于用户的需求,这也表明国内设备商正在跳出对标EOS产品的设计局限以及国内应用市场的强大潜力。大型 SLM 设备将解决了我国大型航空航天精密复杂构件的生产制造瓶颈问题。
▌打印一体化的大型零件有哪些优势和风险
我们以世界首台大规模、大尺寸采用3D打印的型号发动机为例来说明问题。
GE Catalyst是世界上第一台采用3D打印组件的涡轮螺旋桨发动机,新型的结构设计因为3D打印降低了制造复杂性,它将此前通过传统工艺制造的855个零件经过结构优化减少为12个部件。零件的大尺度合并意味着尺寸的急剧增加,传统尺寸的打印机便无法再满足制造需求,这是应用的刚需,打印尺寸不够,设计的再完美也无济于事。
该发动机最具代表性的集成优化部件就是中框组件,该部件在过去的传统制造中包含了300个单独的零件,通过焊接、螺栓连接等方式构成一个部件。工程师通过结构优化,最终将该零件集成在了一起,形成了一个复杂的单一结构,它无法通过传统铸造或机械加工制造,唯有3D打印能够实现一体成型。由此产生的结果在于该部件不再需要装配,不仅减轻了重量,更排除了磨损的可能性,发动机两次维护的时间更是被拉长了1000小时。
除此之外,大尺寸的超燃冲压发动机、火箭发动机、大飞机风扇叶片,此类结构也非常适合一体化打印。这些案例足以说明大尺寸一体化制造的优势,而后续由此带来的燃油效率提升、制造效率提升、供应链结构优化同样非常明显。
然而大尺寸制造的成本也是相当高昂的,金属粉的准备需要以吨计,这确实是非一般用户能玩得起的产品。同时,大尺寸设备的制造风险也很高,在打印过程中出一丁点的问题,零件就可能报废。想象一下,某用户打印了7天的零件,还剩最后某个部位出现了裂纹或卡刀,所造成的损失不仅仅是浪费的材料、金钱,还有时间,更可能因此造成更大的损失。所以此类设备的稳定性更加重要。
2.3D打印集成制造的最佳实例:从855个零件到12个零件的非凡效益
4.多激光无缝拼接的大尺寸粉末床激光熔化自动化设备是怎么工作的?
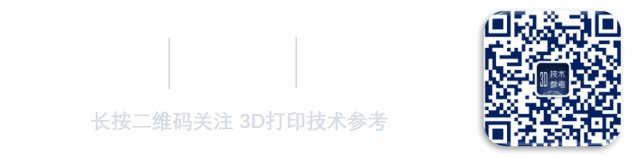