残余应力在现代制造工艺中普遍存在。在许多情况下,它们可以通过设计或后处理工艺来缓解,这些处理工艺通常要么均匀的应用于整个材料(例如退火),要么仅限于近表面区域(例如喷丸处理);或者,可以控制整个材料的残余应力分布,局部诱导拉伸和压缩应力,从而实现宏观性能增强。然而,决定组件中的最终残余应力分布需要在加工或开发材料期间详细控制热分布,这些材料的物理特性和相变以所需的方式改变应力状态。采用这种思路成功开发了角焊缝低温转变(LTT)钢,在奥氏体到马氏体转变期间的体积膨胀导致焊缝中产生压应力,对于冷却过程中理想化的单轴约束,LTT钢表现出马氏体转变过程中压应力的增加以及随着转变温度降低而压缩的残余应力状态。
增材制造以逐层方式顺序制造组件,导致人们重新关注残余应力的管理。增材制造中复杂的热循环通常会产生与传统制造路线不同的非平衡微观结构和性能,需要付出巨大努力才能获得均匀性能。然而,材料沉积和热输入的特定位置性质也提供了操纵局部条件以改变微观结构和性能的机会。这种方法可以被视为材料-结构-性能集成制造的一种形式,其特征是希望获得“在正确位置打印正确的材料”。
原则上,该方法可以包括残余应力分布的设计,例如调整拉伸-压缩不对称性或防止疲劳裂纹萌生和减缓疲劳裂纹扩展。最近的研究调查了在增材制造工艺中使用LTT钢来实现独特且复杂的残余应力状态。然而,工艺条件和相变对所得残余应力分布具有复杂的相互作用影响,其进一步取决于热收缩、塑性应变的积累和退火,以及应力状态和材料特性的温度依赖性。增材制造中的热应力是瞬态的、多轴的,热梯度很高,并且经常经历多个快速加热和冷却循环。为了证明在这些复杂条件下控制残余应力分布的途径,有必要表征加工过程中的温度、相和应力状态。
残余应力与瞬态热应力产生的塑性应变梯度相关。当累积塑性应变与任何可能的弹性位移场不相容时,增材制造组件内的残余应力分布是累积塑性应变梯度的表现。因此,直接观察增材制造过程中的应变演变将对调整加工条件和材料设计以实现针对给定应用量身定制的残余应力分布的能力产生深远影响。
然而,使用传统技术无法实时测量应力演变。增材制造技术前沿注意到,来自橡树岭国家实验室和田纳西大学的研究人员使用原位中子衍射来表征低温相变钢增材制造过程中的瞬态相变和晶格应变演化。结合衍射、红外和模拟数据表明,弹性和塑性应变分布是由面心立方和体心立方相界的运动控制的。相关研究以“Operando neutron diffraction reveals mechanisms for controlled strain evolution in 3D printing”为题发表在今年8月的Nature Communications上。
A. 采用线弧增材制造技术生产低碳钢和低温转变 (LTT250) 钢样品。样品分为三个部分并在其间冷却至室温。B.非原位中子衍射测量显示弹性晶格应变随中心线高度的变化。C构建装置,用于监测SNS加工过程中的温度、相变和晶格应变。D膨胀测量数据显示增材制造 LTT钢的近似相变温度。E操作实验程序示意图,包括三个部分的构建,中间使用主动冷却至室温,然后绘制晶格应变图。
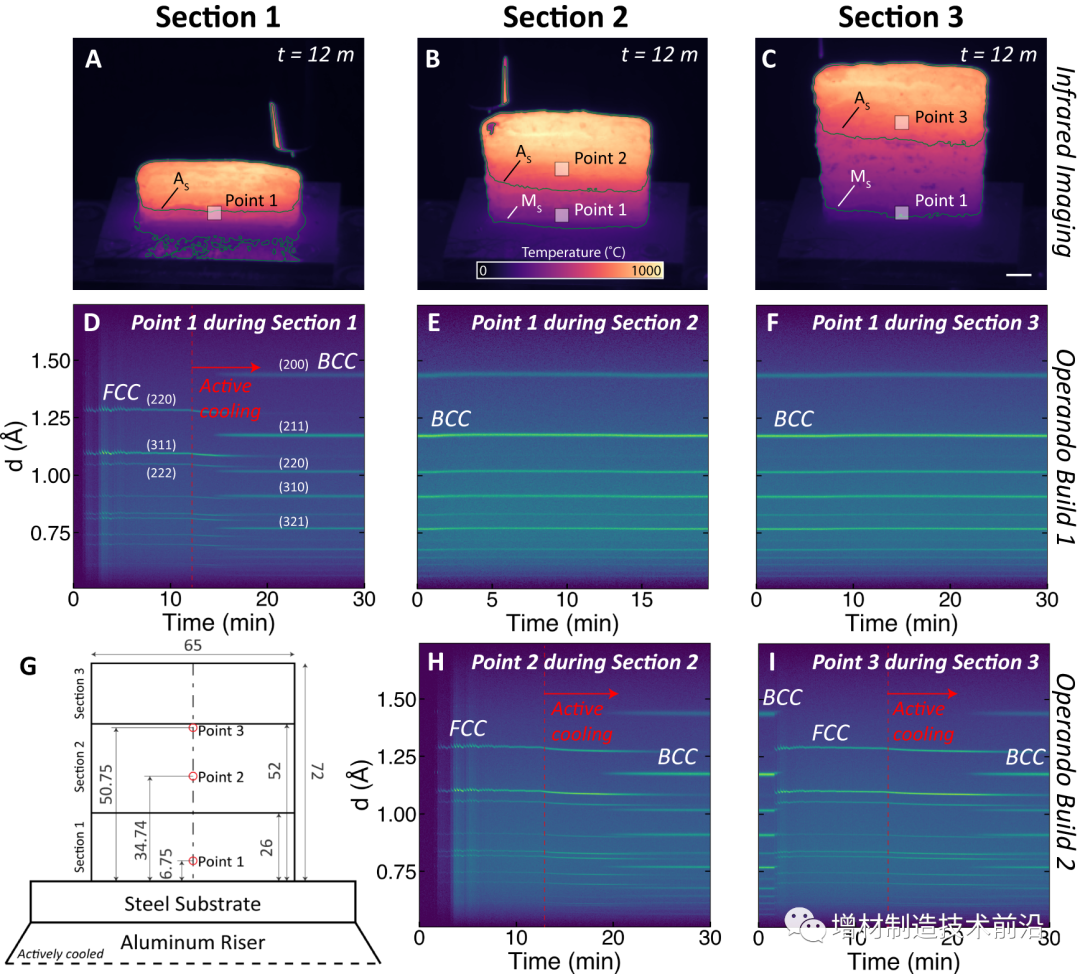
LTT钢制造过程中,使用红外 (IR) 热成像技术测量温度分布随时间的变化,在此期间样品冷却至室温(制造1厘米)。制造过程中,在指定点收集时间分辨中子衍射数据。
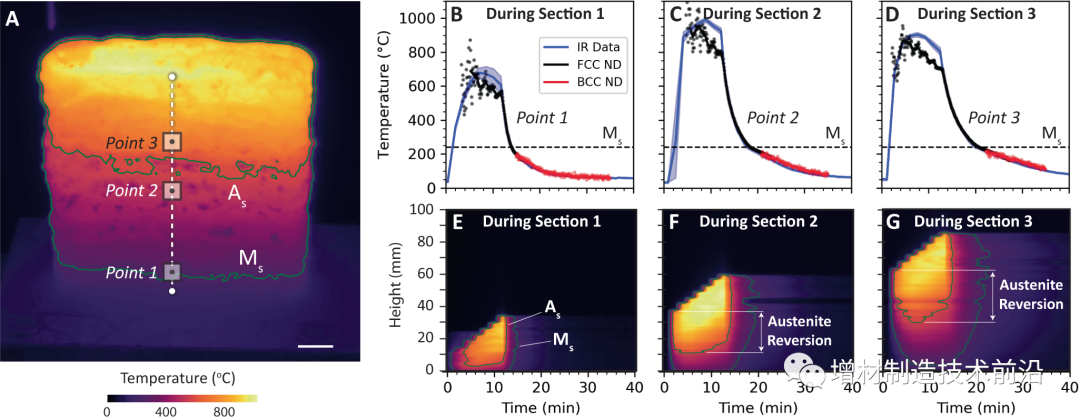
在制造过程中收集每层沉积之间的红外(IR) 数据,并进行校准,清楚地指示与马氏体和奥氏体起始温度相关的等温线(比例为1厘米)
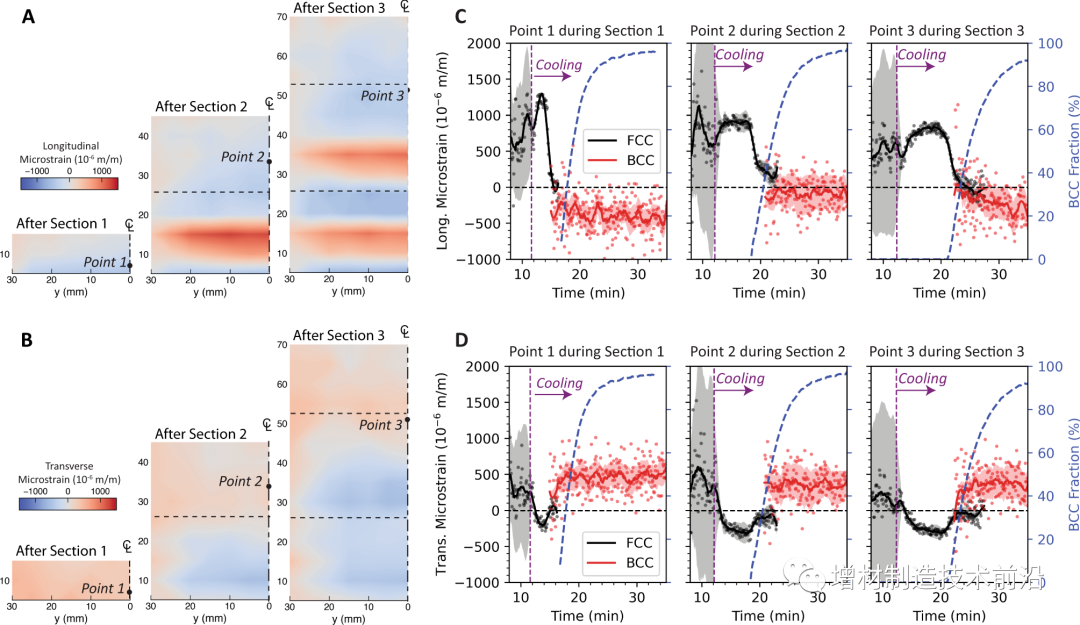
中子衍射晶格应变测量
原位中子表征数据和经过验证的模型结果的结合显示了工艺条件、相变和晶格应变演化之间的相互关系。重要的是,热和机械条件的高时间和空间变化在确定这些影响方面发挥着关键作用,与理想实验相比,LTT钢产生了非常不同的响应。至关重要的是,在存在热梯度的情况下,将先前沉积的材料从BCC重新加热回FCC相场,会在两相之间产生界面,其形状和运动主导弹性和塑性应变演化。由于最终残余应力分布强烈依赖于塑性应变分布的梯度,驱动变形的弹性应变和改变存储塑性应变的热效应发挥着重要作用。
这些观察结果对定制LTT钢的性能具有重大影响。塑性应变的不均匀分布直接影响材料的机械强度和应变硬化响应;弹性残余应变分布改变了材料在每个位置处响应于所施加的载荷而经历的有效应力。根据这些分布的形成机制,很明显它们主要受FCC/BCC界面几何形状的时间演化控制。因此,考虑可能影响临界演变的参数非常重要。如此处所示的简单情况,响应沉积过程的样品加热、冷却和再加热控制界面位置。然而,这种效应还取决于沉积参数和样品边界条件,以及生产部件的几何形状。因此,有多种控制可供调整(焊接参数、道间和层间计时、主动冷却控制)和约束(所需的几何形状、沉积材料的热性能)。本文的结果表明,在计算建模的指导下,可以使用这些控制和约束的平衡来设计和操纵最终材料状态,包括属性和残余应力分布。
总的来说,这项研究为设计增材制造部件中的残余应力状态和性能分布提供了一条新途径。这些发现将能够控制残余应力分布,从而实现提高疲劳寿命或抗应力腐蚀开裂等优点。