南科大&西交大:陶瓷4D打印最新研究进展

陶瓷材料具有优异的机械性能以及耐高温和耐腐蚀性能,因此被广泛应用于航空航天、电气、组织工程以及许多其他领域。由于固有的脆性和高硬度,陶瓷零件的加工一直是困难的。4D打印在高效制造复杂结构陶瓷零部件方面具有巨大潜力
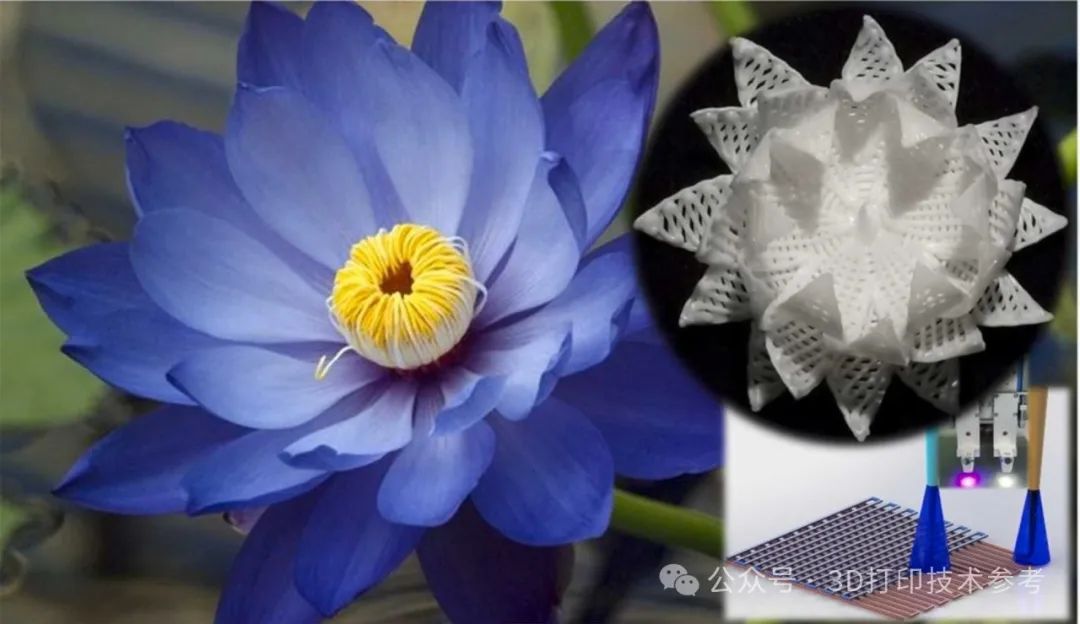
迄今为止,实现陶瓷4D打印主要有两种策略。一种方法是利用烧结过程中的各向异性收缩来产生打印陶瓷部件的形状变化。在这种方法中,采用连续3D打印不同固体含量的陶瓷树脂,在烧结过程中产生各向异性收缩和随之而来的形状变化。借助外力或模具重塑3D打印生坯并结合随后的烧结过程是陶瓷4D打印的另一种有效方法。弹性体衍生陶瓷的4D打印已通过直接墨水写入 (DIW) 和随后的编程步骤实现。可编程自成型可以通过在预拉伸弹性体基底上打印ZrO2纳米粒子增强聚二甲基硅氧烷的设计图案以及随后释放预拉伸来实现,除此之外还可以通过光固化丙烯酸酯陶瓷油墨3D打印制造柔性陶瓷生坯。打印后形状重构可以通过自组装辅助成型和模具辅助成型方法进行。这些重塑的生坯在烧结后可以转化为陶瓷。
https://www.nature.com/articles/s41467-024-45039-y
在这项工作中,研究人员报告了一种可行且高效的制造和设计方法来实现陶瓷的直接4D打印。其开发了用于DLP 3D打印的高光固化陶瓷弹性体浆料和低粘度丙烯酸水凝胶前体。陶瓷弹性体生坯具有高度可拉伸性,能够承受高达700%的拉伸应变。水凝胶作为驱动材料,脱水引起的体积收缩达65%,模量增加40倍。多材料DLP 3D打印技术用于创建图案化的水凝胶陶瓷层压板,其中水凝胶和陶瓷弹性体层形成牢固的界面结合。平面图案层压板在水凝胶脱水的驱动下演变成复杂的3D结构。
多材料3D打印水凝胶陶瓷层压板
陶瓷直接4D打印的设计流程
经过高温脱脂和烧结后,演化出的3D结构变成纯陶瓷结构。为了指导水凝胶-陶瓷层压板的设计,首先开发了一个理论模型来精确捕获脱水引起的水凝胶体积收缩和模量增加,然后将该模型应用到欧拉-伯努利梁理论中以生成设计图建立层压板的弯曲曲率和结构参数之间的关系。实验比较表明,烧结导致弯曲层合板的曲率回缩。通过实验研究和有限元模拟,研究人员将曲率收缩归因于烧结过程中层压板厚度方向的不均匀收缩。通过考虑曲率回缩进一步修改设计图,最后将修改后的设计图与有限元模拟相结合,构建逆向设计流程,以确定使打印的平面图案演变为目标3D陶瓷形状的结构参数。与模具辅助重塑和手动折叠相比,水凝胶脱水驱动的直接4D打印可以更简单、更高效地制造复杂的3D陶瓷物体。
陶瓷直接4D打印的代表性演示
所提出的陶瓷直接4D打印方法可应用于各种陶瓷材料。这种方法在生产复杂3D物体时的高效率和极大的灵活性将突破目前陶瓷结构设计的限制,为陶瓷材料在更广泛的工程领域的应用开辟新途径。研究人员3D打印了起重机、三叶风扇和蝎子,展示了创建复杂3D结构的能力。通过多材料DLP 3D打印技术将水凝胶陶瓷层压板部署在平面图案的不同位置,可以精确地实现弯曲、扭曲、折叠和折纸等局部变形,进而实现各种复杂的形状配置。
主编微信:2396747576(请注明身份); 硕博千人交流Q群:248112776;网址:www.amreference.com
延伸阅读:
2.重大成果:北理工“超大规格金属点阵结构多弧并行3D打印技术与装备”
3.大尺寸、高精度、高质量:突破碳化硅陶瓷3D打印的制造极限
4.2024年首篇Nature增材研究,钛合金3D打印重大突破!