航天领域,并非“万物皆可打印”
www.amreference.com
2019年11月21日,在德国不来梅举办的欧洲航天技术博览会上,一些航天设备制造商表示他们完全看好3D打印将带来制造技术的革命,但也指出大家对这项技术的期望不要过高。这到底是为什么呢?
3D打印经过30多年的发展早已不再是什么新鲜事物,小到儿童玩具和纪念品,大到火箭、飞机的承力结构,都有它的身影。在如今的航天产品制造过程中,可以说采用3D打印早已不是新闻,不采用3D打印才是新闻。
航天领域新旧运营商均积极拥抱3D打印
在液体火箭发动机制造领域,3D打印的应用已经非常普遍。国内民营航天领域,深蓝航天和蓝箭航天率先开启了全3D打印的火箭推力室的制造和实验,两家公司在去年均完成了不同科目的热试车。
中国深蓝航天采用选区激光熔化3D打印工艺制造的液体火箭发动机推力室
国外火箭制造领域,应用3D打印最激进的当数Rocket Lab的电子火箭。该公司的卢瑟福发动机主要部件均采用3D打印,每次打印需要24小时。截至2019年7月,Rocket Lab取得了里程碑式的进展,成功完成了第100台3D打印火箭发动机的制造,其中70台已经投入太空使用。
Rocket Lab 3D打印的火箭发动机
此外,老牌航天公司也积极拥抱3D打印。以美国液发领域最具代表的洛克达因公司为例,该公司的拳头产品之一RL-10系列膨胀循环氢氧发动机,服役超过半个世纪。但一直以来,该发动机的制造成本始终居高不下,单台采购报价曾高达3000万美元。
2017年,洛克达因公司在RL-10C-X项目中使用3D打印制造铜合金推力室和喷注器,替代了原有的钎焊不锈钢管阵列,周期缩短一半,不仅零件数从28个减少到6个,还消灭了上百条焊缝,并经历了超额定功率试车的严峻考验。
含有3D打印核心部件的RL10C-X火箭发动机热火测试
NASA多年来一直在开发面向增材制造的火箭发动机高温合金,并相继有GRCop-84(Cu-8% Cr-4% Nb)和GRCop-42(Cu-4 % Cr-2% Nb)等材料面世。2019年5月,卫星发射公司Virgin Orbit采用GRCop-84铜合金和增减材一体制造工艺为NASA打印了发动机燃烧室,其几何形状与传统设计相同,但工程师能够使用不同材料更快地构建腔室。3D打印为推力室的制造节省了数月时间,热火试验证明基于该工艺制造的复合材料部件与传统制造的性能相一致。
对于复杂零件,采用传统的“车钳铣刨磨”等材料去除方式时,需要逐个加工零部件,再经装配而成,而3D打印能够一体成型,甚至支持不同材料混合打印,免去了繁复的机加工、焊接和装配流程,使成本和制造周期呈几何倍数下降。
在原型阶段,3D打印可节省工装、开模等成本,能快速适应设计团队的变更。而在实际产品阶段,尤其是基于金属粉末和激光烧结技术的成品,不仅能够快速成型出一体化零件,同时其凝固组织亚结构细小,不但没有因3D打印而降低力学性能,反而零件的力学性能普遍优于铸造件,部分甚至接近同成分锻件。
3D打印正逐步介入到安全和可靠性要求最为严格的载人航天器上。
基于该技术的逐步成熟和应用的不断深化,一些企业开始将3D打印应用于载人航天器。
2020年1月19日,SpaceX“龙飞船”高空逃逸测试成功,验证了载人飞船在发射过程中遭遇最极端状况时的逃生能力,这是其进入太空前的最后一个重要测试。“龙飞船”逃逸发动机—SuperDraco也大量采用了3D打印技术。因为发动机紧贴航天员所在的加压舱舱壁,对安全性和可靠性要求极高,而同时其内部几乎所有的冷却通道、喷油头和节流系统采用传统工艺都很难制造,而采用3D打印则可以自由成型。此外,发动机的核心部件—燃烧室,采用镍基超合金实现了选区激光熔化3D打印制造,蜂窝状的燃烧室喉部支撑结构一次成型。
spaceX“自爆”测试成功
除Spacex外,洛克达因公司为“猎户座”制造的姿控发动机喷管延伸段也采用了增材制造技术。该发动机是洛克达因公司首次将3D打印应用在载人飞船上。
“猎户座”姿控 发动机热火测试
但我们也要看到,3D打印发展至今仍有其局限性,在航天领域并不是“万物皆可打印”。
其中的原因首先在于3D打印局限于工作原理,在材料上有适用范围。以液体火箭发动机为例,3D打印对零件的体积和结构都有要求,高能激光束反复熔融过程不亚于对金属进行反复热处理,累计的应力和冷却不均匀等问题会导致大尺寸或承力零件内部出现裂纹和孔隙。
其次,目前的3D打印成品受限于技术水平,很多时候精度有限,在实际装配之前大多离不开传统机械加工。从结构复杂性看,3D打印技术确实可以用来制备结构复杂的大型零件, 然而结构越是复杂,其后续机加工步骤也同样越复杂。因此采用3D打印技术制备复杂结构件对机加工技术同样有强烈的依赖性。对于一些无法进行机加工的复杂结构件来说,即使采用3D打印技术制造出了近净成形的毛坯也没有任何意义。
3D打印的产品尚离不开机加工等后处理手段
还有,某些型号产品进入大批量生产后,相较传统专用工装、模具支持下的批量生产模式,只能逐一制造的3D打印在生产效率上的优势会迅速丧失;而且随着批次的增加,传统设备和模具成本被不断摊平,3D打印产品在成本上也很可能优势不再。即使对于小批量产品,3D打印工艺与常规变形工艺的原材料制备成本差异也很大。
最后,某些结构复杂的3D打印零件也为质检工作带来了新的挑战,比如喷注器,以往只需要在装配前对零件进行逐个检验,但一体成型后只能一次完成,难度陡升。
相比而言,3D打印技术更适合于原材料成本高、战略意义重大、形状结构复杂的金属材料。
END
在航空航天领域的各类型号产品中,除去部分铸造、粉末冶金结构件外,大部分金属结构件都是由板、棒、管等型材和异型材组合而成,这些型材可通过传统的变形工艺得到。因此,通过传统的变形制造工艺,基本可以满足绝大部分金属结构件的制造和性能指标。
只有在结构特别复杂或外形独特、常规方法不便制备、结构件成形一体化(无焊接或其他方式连接等)等需求时,才可能有必要尝试3D打印的方法进行制造。从目前来看,在火箭、卫星等产品制造领域,3D打印是绝佳的补充,暂时称不上彻底颠覆和替代,只有根据产品本身需求和特性合理组合运用增材制造和传统制造,才能最大化两者优势,真正节省时间和成本。
2.采用3D打印工艺--深蓝航天液体火箭发动机整机变推力长程试车圆满成功
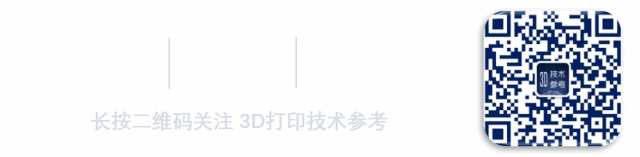